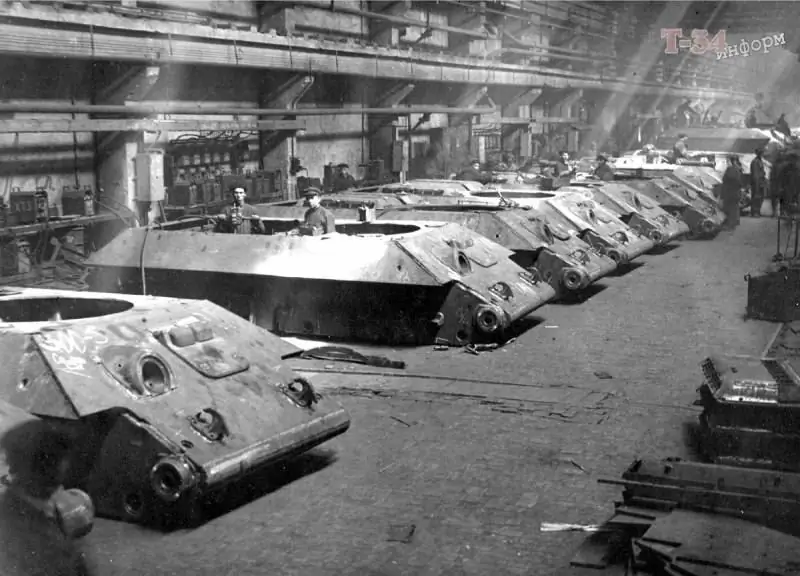
Elos fracos da proteção de aço
Como pode um aumento do tipo avalanche na produção de tanques tão necessários para a frente? O livro de Nikita Melnikov "Indústria de Tanques da URSS durante a Grande Guerra Patriótica" fornece dados sobre o declínio nas condições de recebimento de produtos acabados por representantes militares.
Desde 15 de janeiro de 1942, as fábricas de tanques têm sido muito "liberais" na avaliação da qualidade da fabricação de veículos blindados. Apenas cada décimo tanque médio T-34 e KV pesado à escolha do representante militar foi submetido a uma curta corrida de cinco quilômetros. No caso dos tanques T-60, obviamente havia mais dúvidas, então um em cada cinco tanques leves foi submetido a uma corrida. Ou, talvez, tais máquinas fossem menos necessárias na frente, portanto, eram mais rígidas com elas mesmo na fase de aceitação. Isso confirma indiretamente o controle de tiro do canhão de cada T-60 que saía dos portões das fábricas, enquanto os canhões T-34 e KV eram testados apenas em cada décimo veículo. Foi permitido o envio de tanques às tropas com velocímetros perdidos, motores de giro da torre, interfones caso fossem substituídos por lâmpadas de sinalização, bem como ventiladores da torre. O último ponto, felizmente, só era permitido no inverno.
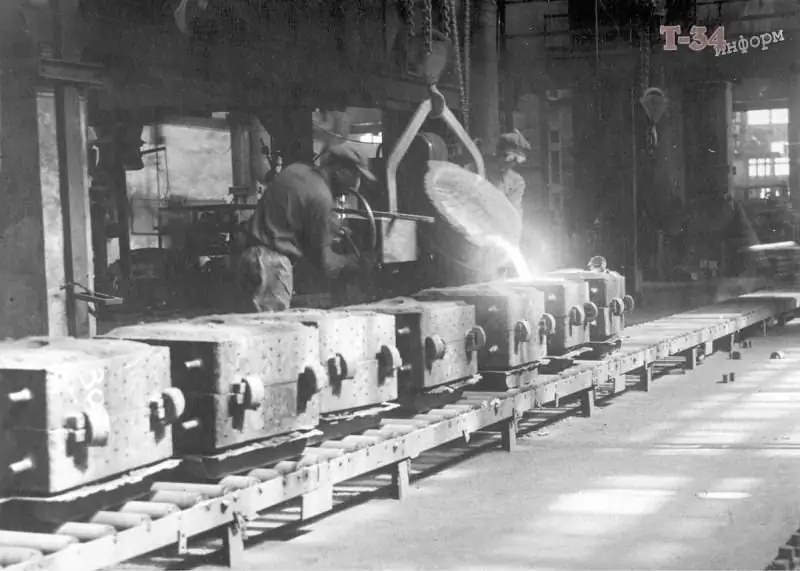
Deve-se notar separadamente que a indústria de tanques já havia lidado com sucesso com os indicadores quantitativos da produção de veículos blindados em meados de 1942. O Uralmash regularmente até excedia os padrões de produção de tanques, e a fábrica de Kirov em Chelyabinsk, apenas de janeiro a março, quadruplicou a produção do motor diesel V-2.
Essas taxas de crescimento da produção foram em grande parte devido a um sério declínio na qualidade dos tanques saindo da linha de montagem. Um exemplo ilustrativo é a 121ª Brigada de Tanques, que, durante um arremesso de 250 quilômetros, perdeu metade de seus pesados KVs devido a avarias. Aconteceu em fevereiro de 1942. Por muito tempo depois disso, a situação não mudou fundamentalmente. No outono de 1942, foram inspecionados 84 tanques KV, que estavam avariados por motivos técnicos, que não funcionavam nem 15 horas de motocicleta. Na maioria das vezes, havia motores defeituosos, caixas de engrenagens quebradas, rolos defeituosos, triplexes inutilizáveis e muitas pequenas falhas. No verão de 1942, até 35% de todos os tanques T-34 foram perdidos não por serem atingidos por projéteis inimigos ou explodidos por uma mina, mas devido à falha de componentes e conjuntos (principalmente motores). Nikita Melnikov em seu trabalho sugere que algumas das perdas podem ser atribuídas ao baixo nível de qualificação da tripulação, mas mesmo levando isso em consideração, a porcentagem de perdas não relacionadas a combate é muito alta. No entanto, esses defeitos do KV e do T-34 podem ser eliminados no campo, às vezes simplesmente substituindo a unidade ou o conjunto. Mas era inútil lutar com a qualidade insatisfatória da blindagem do T-34 na frente - os cascos blindados eram cozidos em aço de baixa viscosidade, que, ao ser atingido por projéteis inimigos, causava rachaduras, delaminação e lascamento. Freqüentemente, rachaduras se formavam em novas máquinas, o que reduzia drasticamente as chances da tripulação de um resultado favorável quando um projétil alemão atingia uma rachadura ou uma área blindada adjacente.
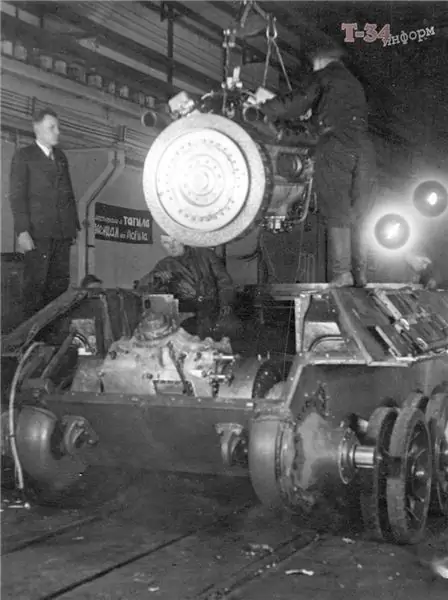
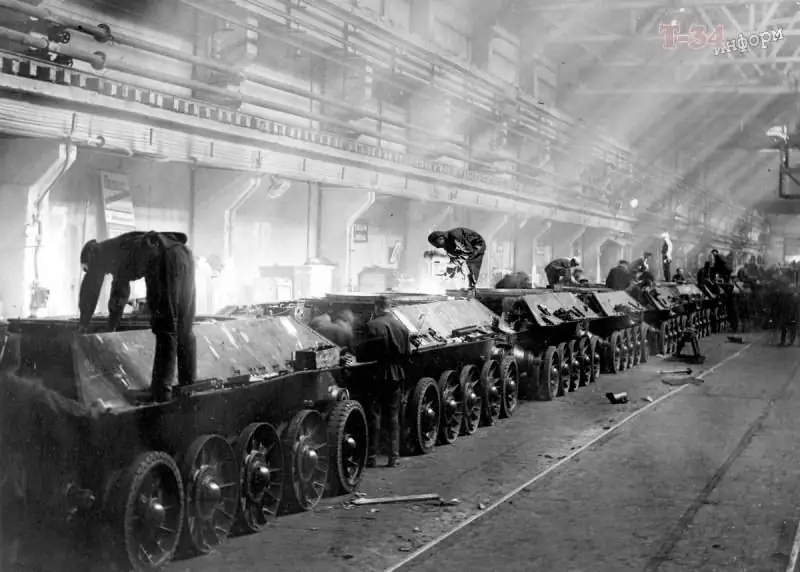
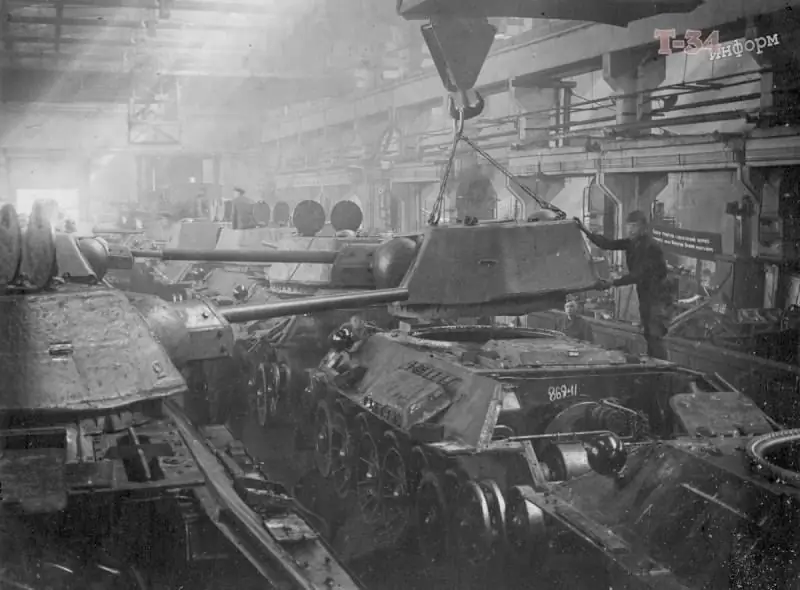
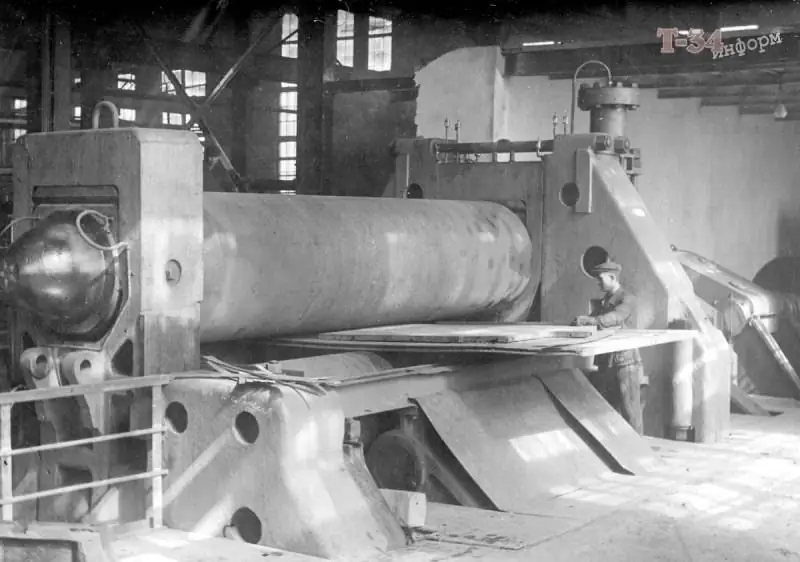
As primeiras chamadas alarmantes sobre a chegada de unidades T-34 com rachaduras soaram em maio de 1942: a fábrica # 183 recebeu reclamações por 13 veículos naquele mês, por 38 tanques em junho e por setenta e dois T-34s nos primeiros dez dias de Julho. … O governo não pôde ficar calado neste caso e, em 5 de junho, o Comitê de Defesa do Estado adotou uma resolução "Sobre a melhoria dos tanques T-34". Ao mesmo tempo, o Ministério Público da URSS foi instruído a investigar as razões dessa queda na qualidade dos tanques.
No decorrer do trabalho, os investigadores, em particular, descobriram numerosos fatos de furto de produtos da dieta de trabalhadores de empresas da indústria de tanques. Os operários da fábrica estavam simplesmente subnutridos. Um exemplo dessa atitude predatória é dado em uma série de materiais sobre Isaac Zaltsman, o mais controverso líder das fábricas de tanques.
Entre as empresas que se "destacaram" na produção de T-34 defeituosos, a famosa fábrica de Nizhny Tagil ficou em primeiro lugar. Além disso, o pico de liberação de produtos defeituosos caiu justamente no momento da liderança do citado Zaltsman. No entanto, o diretor da empresa, como lembramos, não foi rebaixado, mas imediatamente nomeado comissário do povo da indústria de tanques. Obviamente, as autoridades decidiram culpar os mais altos escalões de Vyacheslav Aleksandrovich Malyshev, o primeiro comissário do povo da indústria de tanques da URSS. É verdade que o desânimo veio um ano depois, no verão de 1943, Malyshev foi novamente colocado no lugar de comissário do povo, que manteve até o final da guerra.
O trabalho do Ministério Público no decorrer das obras nas empresas evacuadas da indústria de tanques, além da existência meio faminta dos operários da fábrica, revelou outro problema de qualidade insatisfatória dos tanques - uma grave violação do ciclo de produção.
Simplificação em detrimento da qualidade
Como sabem, a fábrica de Mariupol que leva o nome de Ilyich não pôde ser defendida, acabou nas mãos do inimigo, e com uma massa de equipamentos tecnológicos que não conseguiram evacuar. Foi esta empresa (a única no país) que foi capaz de produzir cascos blindados completos para o T-34 em conformidade com todas as normas. Nos Urais, nem uma única planta poderia oferecer tal coisa, então a equipe de pesquisa do Instituto Blindado (TsNII-48) começou a adaptar as práticas de Mariupol às realidades das fábricas evacuadas. Para a produção de blindagens de alta qualidade nos volumes exigidos pela GKO, havia uma escassez aguda de fornos térmicos, então o instituto desenvolveu um novo ciclo de endurecimento de peças de blindagem. Em Mariupol, a camada de blindagem primeiro foi endurecida, depois em alta temporada, e novamente endurecida. Finalmente, seguiram-se férias baixas. Para acelerar a produção, o primeiro endurecimento foi inicialmente cancelado e, em seguida, o revenido alto, que afeta diretamente a tenacidade do aço blindado e reduz a probabilidade de rachaduras. Além disso, entre as medidas necessárias, de acordo com os especialistas do Armor Institute, a exigência era carregar não uma, mas imediatamente quatro ou cinco fileiras de placas de blindagem no forno térmico. Naturalmente, isso acabou sendo muito mais rápido, mas a qualidade final das lajes era muito heterogênea. Curiosamente, o Armored Institute decidiu posteriormente cancelar o procedimento de revenido baixo, o que reduz as tensões residuais do metal, que mais uma vez não deixou de afetar negativamente a formação de trincas.
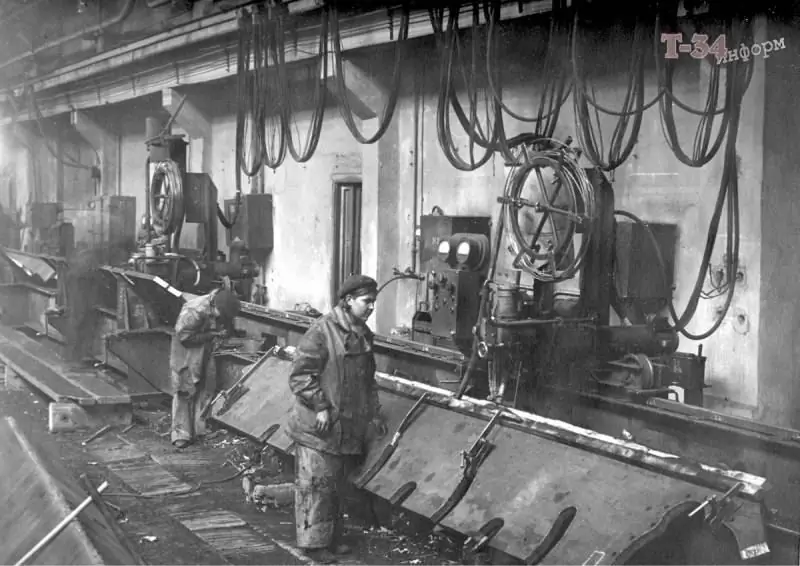
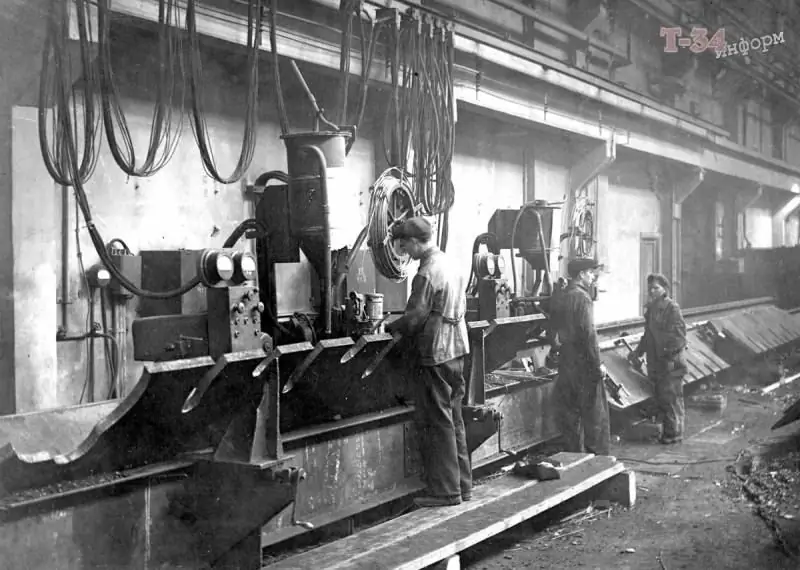
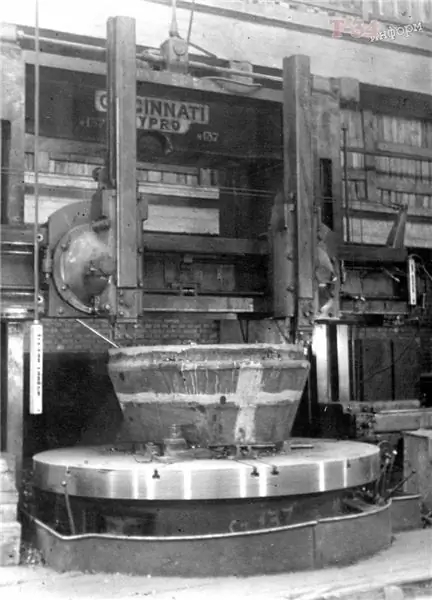
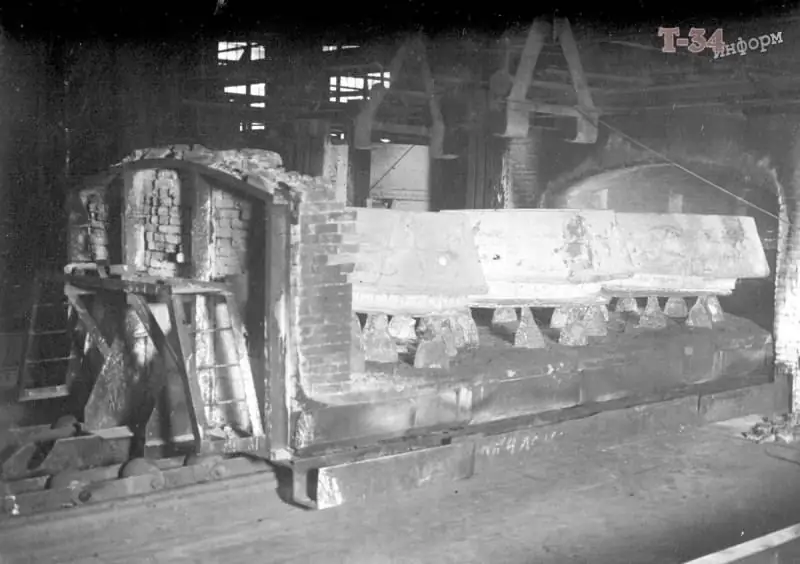
Não se pode cortar aço endurecido com cortadores a gás - esta tese é conhecida por todos, mas as realidades da produção de cascos blindados T-34 obrigaram a recorrer a este método impopular. A ponta era em aço 8C, que se expandia após a têmpera e, naturalmente, isso obrigava os operários a cortá-la com queimadores de alta temperatura. O ponto de endurecimento da armadura na área de corte foi perdido.
Não vale a pena argumentar que as recomendações para melhoria do processo de produção foram negativas apenas para a qualidade da armadura. Assim, uma verdadeira inovação na montagem dos cascos dos tanques T-34 foi a soldagem das placas de blindagem "em um espinho" ao invés das antigas "na fechadura" e "em um quarto". Agora as partes de acasalamento não se cortavam, mas parcialmente se sobrepunham. Somente esta decisão reduziu seriamente o volume de horas-máquina por caso de 198,9 para 36.
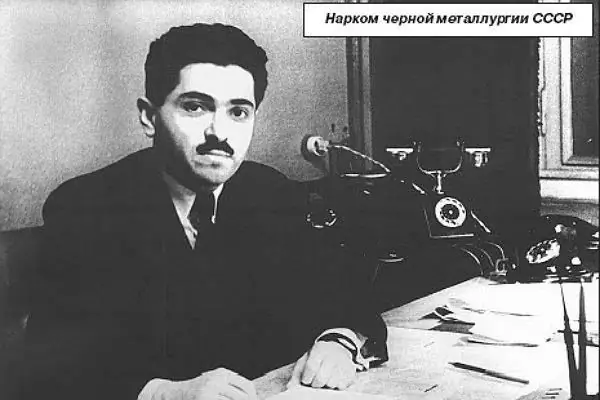
O principal fornecedor de chapas de aço com defeito para as fábricas de T-34 era a planta Novo-Tagil do Comissariado do Povo de Metalurgia Ferrosa. A princípio, foi interrompido por suprimentos da fábrica de Mariupol e, quando mudou para a sua própria, uma torrente de reclamações veio da frente e das fábricas. Em particular, na composição da blindagem 8C deste empreendimento havia sérias discrepâncias com as especificações técnicas (TU) no conteúdo de carbono, fósforo e silício. Em geral, houve dificuldades com o TU. O Comissariado do Povo da Metalurgia Ferrosa não concordou em preservar a TU de acordo com os padrões da Mariupol, nos quais o fósforo, em particular, não deveria ser superior a 0,035%. No início de novembro de 1941, o Comissário do Povo da Metalurgia Ferrosa Ivan Tevosyan aprovou novos padrões para o fósforo, que aumentaram o teor possível para 0,04%, e de 4 de abril para 0,045%. Vale ressaltar que os historiadores ainda não têm consenso sobre este, é claro, um fator importante na qualidade do aço blindado. Nikita Melnikov, em particular, menciona que a fábrica Novo-Tagil, ao contrário, em meados de 1942 reduziu a proporção de fósforo de 0,029% para 0,024%. Parece que diferentes cientistas encontraram diferentes razões para o aparecimento de T-34s defeituosos na frente. Seja como for, as normas indicadas para o teor de elementos químicos na composição do aço, por vezes, não eram observadas. Era difícil para as fábricas estabelecer uma uniformidade simples dos produtos laminados fornecidos. A promotoria também revelou que nas empresas de metalurgia ferrosa em fornos de sola aberta, o aço blindado era "malpassado" - em vez de 15-18 horas na realidade, não mais que 14 horas.
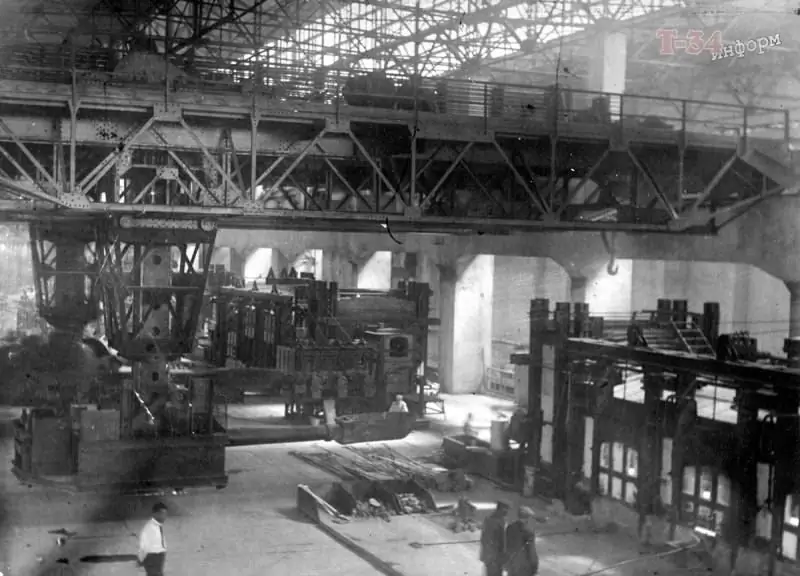
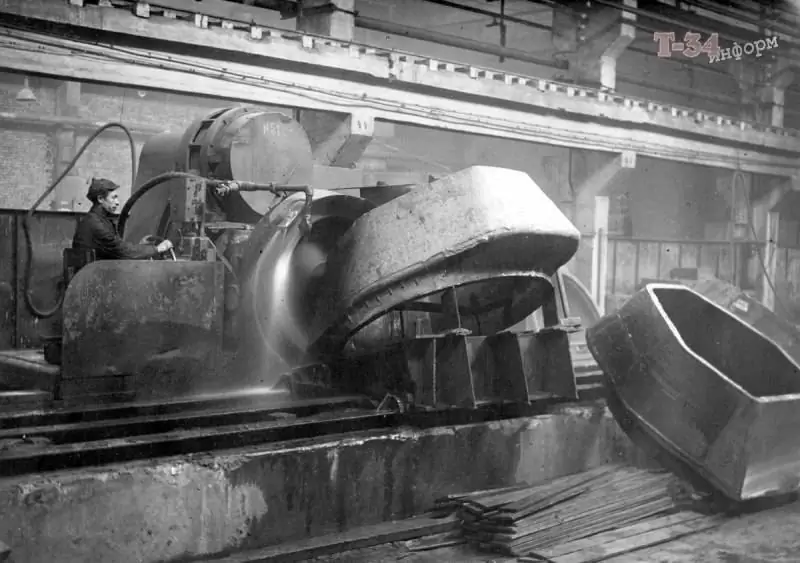
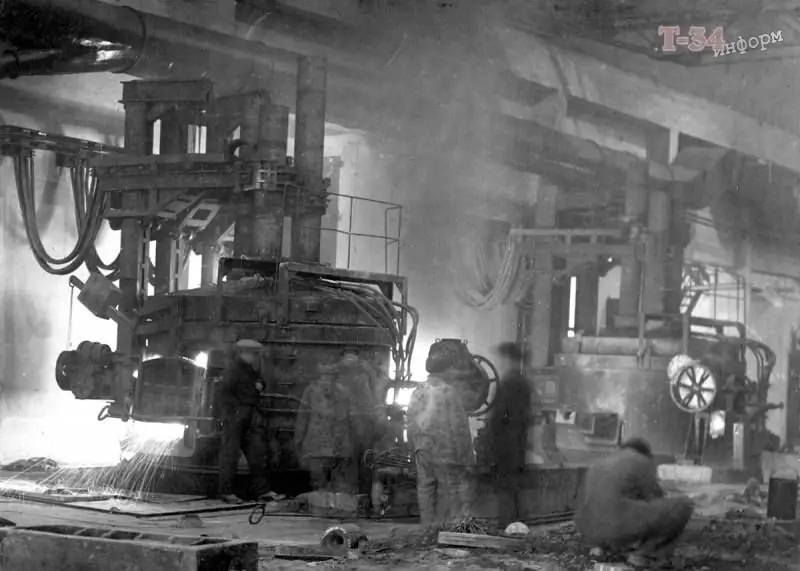
Quando as informações sobre as causas das rachaduras nos cascos do T-34 chegaram a Molotov, os comissariados populares da metalurgia ferrosa e da indústria de tanques começaram a transferir a responsabilidade uns para os outros. Por um lado, o principal motivo era o alto teor de fósforo nas placas de blindagem, por outro, graves violações da tecnologia de produção de cascos nas fábricas de tanques.
Como resultado, TsNII-48 estava envolvido no trabalho de combate a rachaduras no T-34 (embora fosse indiretamente culpado de seu aparecimento). O conjunto de medidas propostas pelo instituto somente no final de 1943 permitiu eliminar alguns dos comentários. E a melhoria da qualidade da produção de aço nas empresas de metalurgia ferrosa permitiu reduzir a proporção de rejeitos de 56,25% em 1942 para 13,30% em 1945. Os empreendimentos não atingiram o patamar próximo a 100% até o final da guerra.