O fato da existência de um batiscafo, que conseguiu conquistar o abismo mais profundo, atesta a possibilidade técnica de criação de veículos tripulados para mergulho em qualquer profundidade.
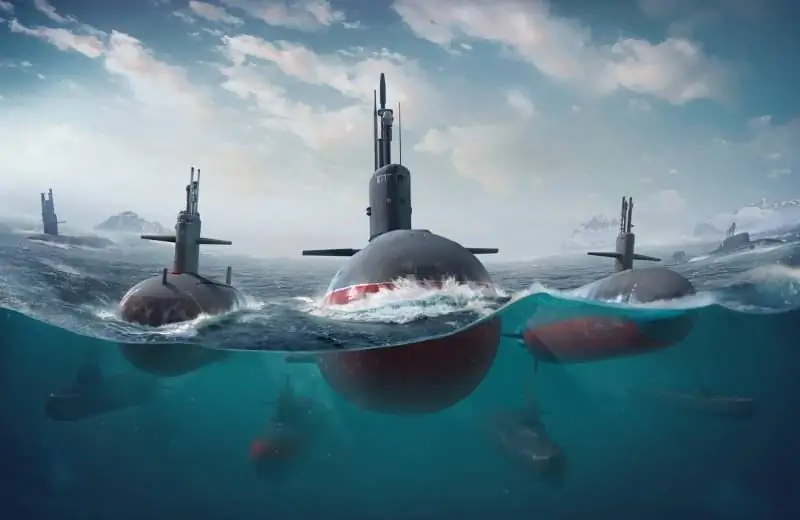
Por que nenhum dos submarinos modernos está nem perto de ser capaz de mergulhar - mesmo a 1000 metros?
Há meio século, o batiscafo, montado a partir dos meios improvisados de aço padrão e plexiglass, chegou ao fundo da Fossa Mariana. E eu poderia continuar meu mergulho se houvesse grandes profundidades na natureza. A profundidade do projeto seguro para Trieste foi de 13 quilômetros!
Mais de 3/4 da área do Oceano Mundial cai na zona abissal: um leito oceânico com profundidades de mais de 3.000 m. Espaço operacional genuíno para a frota de submarinos! Por que ninguém está aproveitando essas oportunidades?
A conquista de grandes profundidades nada tem a ver com a resistência do casco dos "Sharks", "Boreyev" e "Virginia". O problema é diferente. E o exemplo do batiscafo "Trieste" não tem absolutamente nada a ver com isso.
Eles são semelhantes, como um avião e um dirigível
O batiscafo é um "flutuador". Vagão tanque com gasolina, com uma gôndola da tripulação fixada embaixo dele. Quando o lastro é levado a bordo, a estrutura adquire flutuabilidade negativa e afunda em profundidade. Quando o lastro é lançado, ele retorna à superfície.
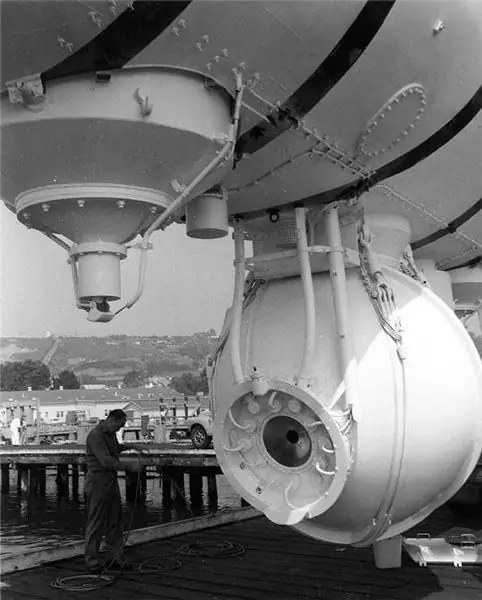
Ao contrário do batiscafo, os submarinos precisam alterar repetidamente a profundidade de estar sob a água durante um mergulho. Em outras palavras, o submarino tem a capacidade de alterar repetidamente a reserva de flutuabilidade. Isso é conseguido enchendo os tanques de lastro com água do mar, que são soprados com ar durante a subida.
Normalmente, os barcos usam três sistemas de ar: ar de alta pressão (HPP), pressão média (HPA) e ar de baixa pressão (HPP). Por exemplo, em navios americanos modernos movidos a energia nuclear, o ar comprimido é armazenado em cilindros a 4.500 psi. polegada. Ou, humanamente, cerca de 315 kg / cm2. No entanto, nenhum dos sistemas que consomem ar comprimido usa VVD diretamente. Quedas repentinas de pressão causam congelamento intenso e bloqueio das válvulas, ao mesmo tempo criando o perigo de explosões de compressão dos vapores de óleo no sistema. O uso generalizado de VVD sob pressão acima de 300 atm. criaria perigos inaceitáveis a bordo do submarino.
O VVD através de um sistema de válvulas redutoras de pressão é fornecido aos consumidores na forma de VVD sob uma pressão de 3000 lb. por sq. polegadas (aproximadamente 200 kg / cm2). É com esse ar que explodem os tanques principais de lastro. Para garantir o funcionamento dos demais mecanismos do barco, o lançamento de armas, assim como o sopro do trim e equalização dos tanques, utiliza-se ar "de trabalho" a uma pressão ainda mais baixa de cerca de 100-150 kg / cm2.
E é aqui que as leis do drama entram em jogo!
Com um mergulho nas profundezas do mar a cada 10 metros, a pressão aumenta em 1 atmosfera
A uma profundidade de 1500 m, a pressão é de 150 atm. A uma profundidade de 2.000 m, a pressão é de 200 atm. Isso corresponde exatamente ao valor máximo de IRR e IRR em sistemas submarinos.
A situação é agravada pelos volumes limitados de ar comprimido a bordo. Principalmente depois de o barco estar muito tempo submerso. A uma profundidade de 50 metros, as reservas disponíveis podem ser suficientes para deslocar a água dos tanques de lastro, mas a uma profundidade de 500 metros, isso é suficiente apenas para soprar 1/5 de seu volume. As profundidades profundas são sempre um risco e deve-se proceder com o máximo de cautela.
Hoje em dia, existe a possibilidade prática de criar um submarino com casco projetado para uma profundidade de mergulho de 5.000 metros. Mas soprar os tanques em tal profundidade exigiria ar sob uma pressão de mais de 500 atmosferas. Projetar tubulações, válvulas e conexões projetadas para essa pressão, mantendo seu peso razoável e eliminando todos os riscos associados, é hoje uma tarefa tecnicamente insolúvel.
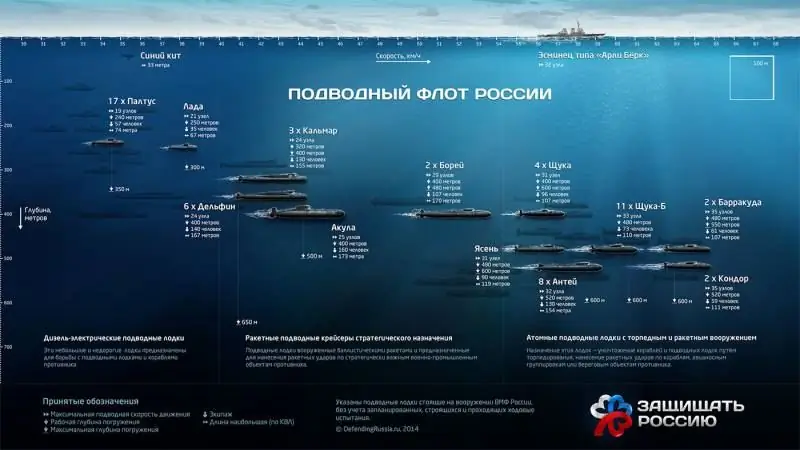
Os submarinos modernos são construídos com base no princípio de um equilíbrio razoável de desempenho. Por que construir um casco de alta resistência que pode suportar a pressão de uma coluna de água com um quilômetro de comprimento quando os sistemas de revestimento são projetados para profundidades muito mais rasas? Tendo afundado um quilômetro, o submarino estará condenado de qualquer maneira.
No entanto, esta história tem seus próprios heróis e párias.
Os submarinistas americanos são considerados forasteiros tradicionais no campo do mergulho em alto mar
Por meio século, os cascos dos barcos americanos foram feitos de uma única liga HY-80 com características muito medíocres. High-yield-80 = 80.000 psi liga de alto rendimento polegada, que corresponde ao valor de 550 MPa.
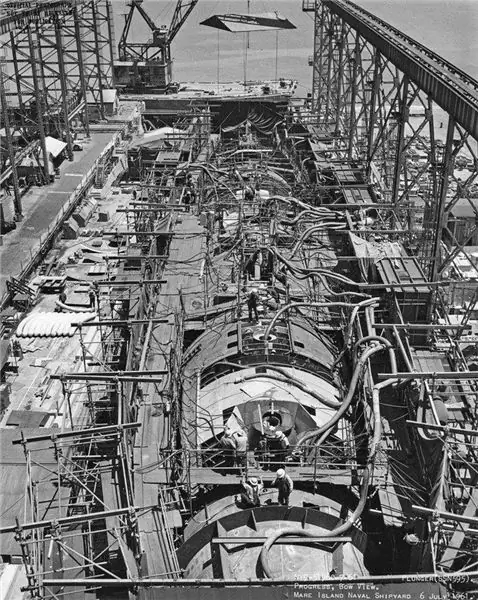
Muitos especialistas expressam dúvidas sobre a adequação de tal solução. Devido ao casco fraco, os barcos são incapazes de explorar totalmente as capacidades dos sistemas de subida. Que permitem o sopro de tanques em profundidades muito maiores. Estima-se que a profundidade de trabalho de submersão (profundidade em que o barco pode ficar por muito tempo, fazendo qualquer manobra) para submarinos americanos não ultrapasse 400 metros. A profundidade máxima é de 550 metros.
A utilização do HY-80 permite reduzir o custo e agilizar a montagem das estruturas do casco, entre as vantagens, as boas qualidades de soldagem desse aço sempre foram chamadas.
Para os ardentes céticos, que declararão imediatamente que a frota do "inimigo em potencial" é maciçamente reabastecida com lixo não combatível, o seguinte deve ser observado. Essas diferenças no ritmo de construção naval entre a Rússia e os Estados Unidos se devem não tanto ao uso de aços de qualidade superior para nossos submarinos, mas a outras circunstâncias. Qualquer forma.
No exterior, sempre se acreditou que os super-heróis não são necessários. As armas subaquáticas devem ser tão confiáveis, silenciosas e numerosas quanto possível. E há alguma verdade nisso.
Komsomolets
O evasivo "Mike" (K-278 de acordo com a classificação da OTAN) estabeleceu um recorde absoluto de profundidade de mergulho entre submarinos - 1.027 metros.
A profundidade máxima de imersão dos "Komsomolets" de acordo com os cálculos foi de 1250 m.
Entre as principais diferenças de projeto, incomuns para outros submarinos domésticos, há 10 tanques sem anel localizados dentro de um casco durável. Possibilidade de disparar torpedos de grandes profundidades (até 800 metros). Pod de fuga pop-up. E o principal destaque é o sistema de emergência para insuflação de tanques com o auxílio de geradores a gás.
O corpo feito de liga de titânio tornou possível perceber todas as vantagens inerentes.
O titânio em si não foi uma panacéia para conquistar as profundezas do mar. O principal na criação dos Komsomolets para águas profundas foi a qualidade de construção e a forma de um casco sólido com um mínimo de buracos e pontos fracos.
A liga de titânio 48-T com ponto de escoamento de 720 MPa foi apenas ligeiramente superior em resistência ao aço estrutural HY-100 (690 MPa), a partir do qual os submarinos SeaWolf foram feitos.
As outras "vantagens" descritas da caixa de titânio na forma de propriedades magnéticas baixas e sua menor suscetibilidade à corrosão não valiam por si mesmas o investimento. A magnetometria nunca foi um método prioritário para a detecção de barcos; debaixo de água, tudo é decidido pela acústica. E o problema da corrosão marinha foi resolvido por duzentos anos por métodos mais simples.
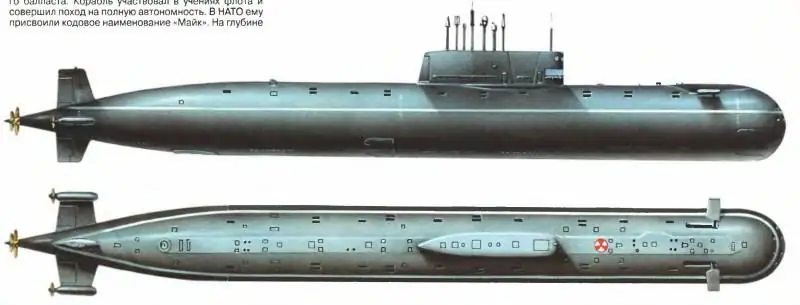
O titânio do ponto de vista da construção naval submarina doméstica tinha DUAS vantagens reais:
a) menos densidade, o que significa um corpo mais leve. As reservas emergentes foram gastas em outros itens de carga, por exemplo, usinas de maior potência. Não é por acaso que os submarinos com casco de titânio (705 (K) "Lira", 661 "Anchar", "Condor" e "Barracuda") foram construídos como conquistadores de velocidade.;
b) Entre todos os aços e ligas de alta resistência A liga de titânio 48-T revelou-se a mais avançada tecnologicamente no processamento e montagem de estruturas de casco.
"Mais avançado tecnologicamente" não significa simples. Mas as qualidades de soldagem do titânio pelo menos permitiram a montagem de estruturas.
A Overseas teve uma visão mais otimista do uso do aço. Para a fabricação de cascos para novos submarinos do século XXI, foi proposto o aço de alta resistência da marca HY-100. Em 1989, os Estados Unidos lançaram as bases para o SeaWolfe líder. Depois de dois anos, o otimismo diminuiu. O casco do SeaWolfe teve de ser desmontado e reiniciado.
Muitos problemas já foram resolvidos, e ligas de aço equivalentes em propriedades ao HY-100 estão encontrando aplicações mais amplas na construção naval. De acordo com alguns relatórios, esse aço (WL = Werkstoff Leistungsblatt 1.3964) é usado na fabricação de um casco durável de submarinos alemães não nucleares "Tipo 214".
Existem ligas ainda mais fortes para a construção de caixas, por exemplo, liga de aço HY-130 (900 MPa). Mas por causa das propriedades de soldagem pobres, os construtores navais consideraram o uso do HY-130 impossível.
Ainda não há notícias do Japão.
耐久 significa força de rendimento
Como diz o velho ditado: "Tudo o que você faz bem, sempre há um asiático que o faz melhor."
Há muito pouca informação em fontes abertas sobre as características dos navios de guerra japoneses. No entanto, os especialistas não são impedidos pela barreira do idioma ou pelo sigilo paranóico inerente à segunda marinha mais forte do mundo.
A partir das informações disponíveis, conclui-se que os samurais, junto com os hieróglifos, usam amplamente as designações inglesas. Na descrição dos submarinos, consta a abreviatura NS (Naval Steel - naval steel), combinada com os índices digitais 80 ou 110.
No sistema métrico, "80" ao designar um tipo de aço provavelmente significa um limite de escoamento de 800 MPa. O aço mais resistente NS110 tem um limite de elasticidade de 1100 MPa.
Do ponto de vista americano, o aço padrão para submarinos japoneses é o HY-114. Melhor e mais durável - HY-156.
Cena muda
"Kawasaki" e "Mitsubishi Heavy Industries" sem qualquer promessa e "Poseidons" aprenderam a fazer cascos com materiais que antes eram considerados incompatíveis e impossíveis na construção de submarinos.
Os dados fornecidos correspondem a submarinos obsoletos com uma instalação independente de ar do tipo "Oyashio". A frota é composta por 11 unidades, das quais as duas mais antigas, que entraram ao serviço em 1998-1999, foram transferidas para a categoria de unidades de formação.
"Oyashio" tem um design de casco duplo misto. A suposição mais lógica é que a seção central (casco forte) é feita do aço mais durável NS110, um design de casco duplo é usado na proa e na popa do barco: um casco leve e aerodinâmico feito de NS80 (pressão interna = externa pressão), cobrindo os tanques de lastro principais fora do casco forte. …
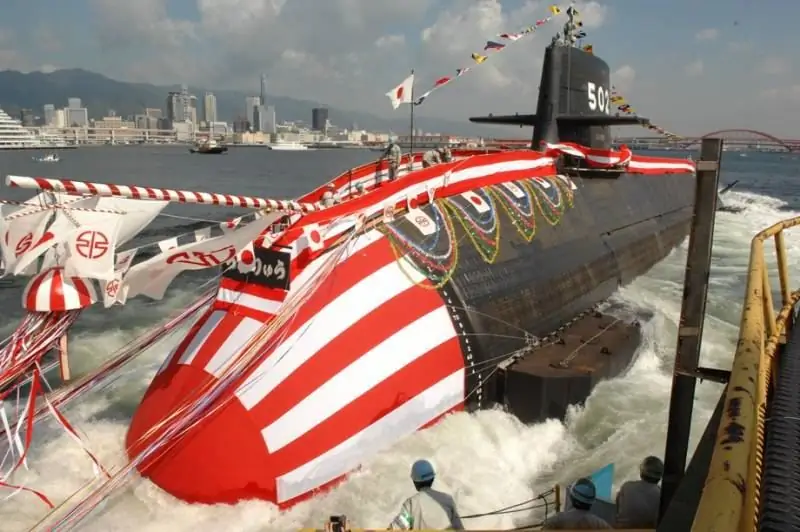
Os submarinos japoneses modernos do tipo "Soryu" são considerados "Oyashio" aprimorados, embora mantendo as soluções de design básicas herdadas de seus predecessores.
Com seu robusto casco de aço NS110, a profundidade de trabalho da Soryu é estimada em pelo menos 600 metros. O limite é 900.
Dadas as circunstâncias apresentadas, as Forças de Autodefesa japonesas possuem atualmente a mais profunda frota de submarinos de combate.
Os japoneses "espremem" tudo o que é possível a partir do disponível. Outra questão é o quanto isso ajudará em um conflito naval. Para o confronto nas profundezas do mar, é necessária uma usina nuclear. O lamentável "meio-termo" japonês com o aumento da profundidade de trabalho ou a criação de um "barco movido a bateria" (o submarino Oryu que surpreendeu o mundo) parece uma cara boa para um jogo ruim.
Por outro lado, a atenção tradicional aos detalhes sempre permitiu que os japoneses tivessem uma vantagem sobre o inimigo. O surgimento de uma usina nuclear para a Marinha Japonesa é uma questão de tempo. Mas quem mais no mundo possui tecnologias para fabricar caixas ultra-resistentes de aço com limite de elasticidade de 1100 MPa?