A guerra é conhecida por ser o melhor motor do progresso. A indústria de tanques da União Soviética deu um salto qualitativo vertiginoso em apenas alguns anos de guerra. A verdadeira coroa disso foram os tanques da série IS.
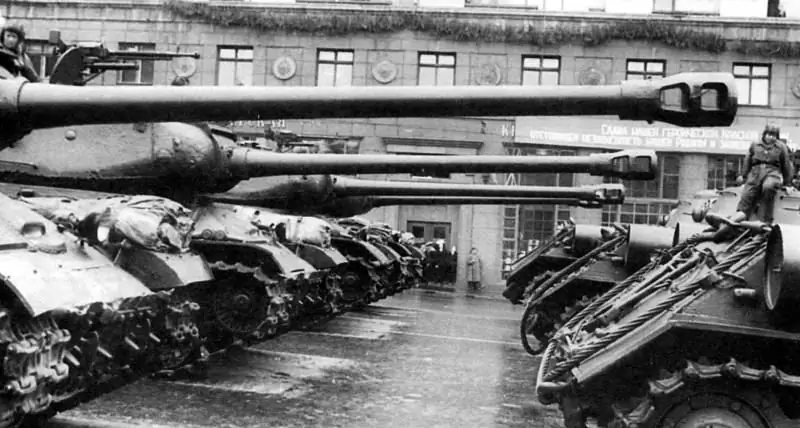
Receitas magnitogorsk
Na parte anterior da história, era sobre a armadura fundida de alta dureza 70L usada para as torres dos tanques IS. Os desenvolvedores da armadura do TsNII-48 estavam longe de ser a primeira experiência na criação de proteção para tanques pesados.
Antes do Kursk Bulge, que se tornou um catalisador para o desenvolvimento da construção de tanques pesados domésticos, o principal objeto de modernização era o tanque KV. Inicialmente, todo o trabalho visava reduzir a proporção de escassos aditivos de liga na composição da armadura. Até mesmo o nome em TsNII-48 veio com um apropriado - aço com liga econômica. A blindagem original da marca FD-7954, com a qual o tanque KV entrou na Grande Guerra Patriótica, continha, de acordo com as exigências técnicas, até 0,45% de molibdênio, 2,7% de níquel e cromo.
No final de 1941, um grupo de pesquisadores liderado por Andrei Sergeevich Zavyalov no Armored Institute criou uma receita para o aço FD-6633 ou 49C, em que o molibdênio exigia não mais que 0,3%, cromo - até 2,3% e níquel - até 1, 5%. Considerando que os tanques da série KV do segundo semestre de 1941 a 1943 foram arrecadados cerca de 4 mil exemplares, pode-se imaginar a quantidade de economia real na liga de metais.
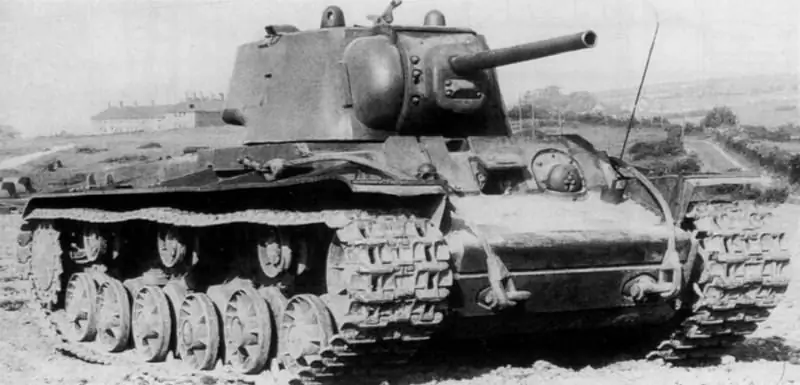
O segredo do sucesso
O segredo do sucesso dos metalúrgicos está no estudo dos parâmetros de formação da fratura fibrosa da armadura - principal parâmetro da resistência do projétil. Descobriu-se que você pode dispensar uma proporção significativa de elementos de liga simplesmente mudando a taxa de resfriamento da armadura durante a têmpera. Mas isso é simples em palavras - quantos experimentos preliminares e derretimentos os metalúrgicos tiveram que fazer, apenas os arquivos agora classificados serão capazes de dizer.
Na Metalúrgica Magnitogorsk, em 1941, foram obtidos os primeiros protótipos de aço 49C, que não eram inferiores à tradicional armadura de "pré-guerra". Em particular, o bombardeio do canhão de 76 mm mostrou total conformidade com os requisitos táticos do tanque. E desde 1942, apenas a armadura com o nome 49C foi usada para a série KV. Vale lembrar que o consumo de cromo, molibdênio e níquel diminuiu significativamente.
A busca por novas formulações de blindagens para equipamentos pesados não parou por aí. Em 1942, o aço GD-63-3 foi “soldado”, totalmente desprovido dos escassos cromo e níquel. Em certa medida, o níquel foi substituído pelo manganês - sua participação aumentou mais de três vezes (até 1,43%). Protótipos da nova armadura foram disparados. E eles acabaram sendo bastante adequados para uso em massa no projeto do KV. Mas os tanques Klim Voroshilov com blindagem de dureza média estavam se aposentando. E o lugar dos veículos pesados foi ocupado pelos veículos “Joseph Stalin” com blindagem de alta dureza.
Armadura enrolada 51C
Se a blindagem 70L para a torre IS-2 pudesse ser lançada, esse truque não funcionaria com as partes do casco do tanque. Aqui, os engenheiros enfrentaram dois problemas ao mesmo tempo - a criação de uma armadura de alta dureza de grande espessura e a necessidade de soldá-la em um casco acabado.
Todos os interessados provavelmente já conhecem os problemas causados pela soldagem da armadura do T-34 - há grande probabilidade de trincas na área de soldas. O IS-2 não foi exceção. E seu corpo deveria originalmente ser cozido a partir de partes finalmente tratadas termicamente.
Percebendo quais dificuldades e perigos essa solução tecnológica traria para uma operação militar, os especialistas do TsNII-48 mudaram o ciclo de produção do tanque. Como resultado, em 1943, na Ural Heavy Machine Building Plant e na Chelyabinsk Plant No. 200, o casco IS-2 foi decidido a ser cozido a partir de placas de blindagem que haviam passado apenas um período de férias depois de laminar. Ou seja, na verdade, o casco de um tanque pesado foi montado com aço "bruto". Isso reduziu bastante os defeitos de soldagem na armadura laminada de alta dureza 51C.
O tratamento térmico final por aquecimento antes da têmpera foi realizado já no corpo soldado do tanque, tendo-o previamente reforçado com escoras internas. O corpo foi mantido no forno por três horas. E então, em dispositivos especiais, eles foram transferidos para um tanque de têmpera de água e mantidos nele por 15 minutos. Além disso, a temperatura da água no tanque de resfriamento aumentou de 30 para 55 ° C. A temperatura da superfície do corpo após ser removido da água era de 100-150 ° С. E isso não é tudo.
Após a têmpera, o corpo foi imediatamente submetido a um baixo revenido em um forno circulante a uma temperatura de 280-320 ° C com retenção após atingir essa temperatura por 10-12 horas. O baixo temperamento das torres fundidas da blindagem 70L foi realizado de forma semelhante. Curiosamente, o controle de rachaduras nos cascos experimentais IS-2 durou quatro meses, quando os primeiros tanques de produção deixaram os portões da fábrica.
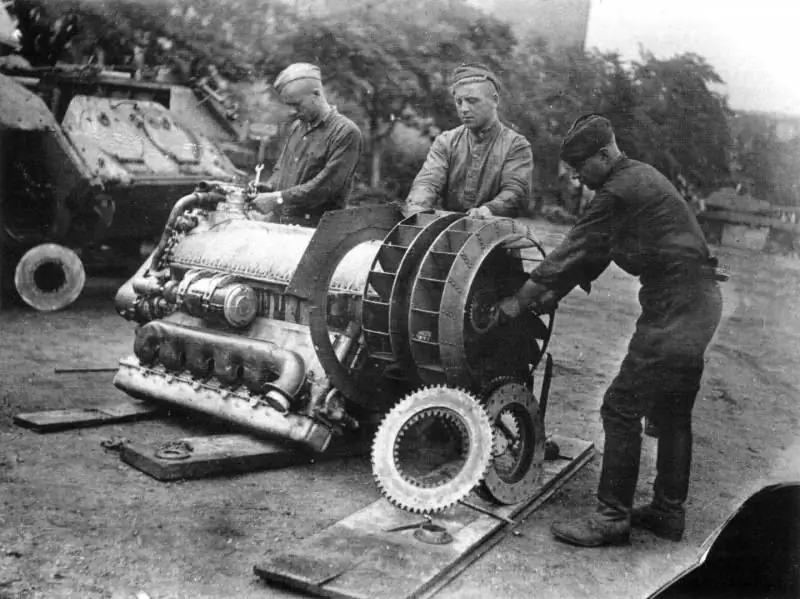
Composição química
Qual foi a blindagem 51C enrolada que se tornou a principal para o IS-2, ISU-122 e ISU-152? É um aço de têmpera profunda para grandes espessuras de blindagem com a seguinte composição química (%):
C 0, 18-0, 24
Mn 0, 70-1, 0
Si 1, 20-1, 60
Cr 1, 0-1, 5
Ni 3,0-3,8
Mo 0, 20-0, 40
P ≤ 0,035
S ≤0,035.
Em comparação com a armadura fundida 70L, o aço laminado 51C apresentou maior proporção de molibdênio e níquel, o que garantiu aumento da temperabilidade até 200 mm. Quando os cascos dos tanques pesados foram disparados com munições de 88 mm, descobriu-se que a armadura de alta dureza era muito superior em durabilidade aos seus predecessores de dureza média. A questão de colocar a armadura enrolada 51C foi resolvida imediatamente.
Soldagem inteligente
Uma importante contribuição para o sucesso do desenvolvimento da produção de blindagem de tanques da série IS foi feita pela soldagem automática do aço sob uma camada de fluxo. Como era impossível transferir todo o processo de fabricação de um casco blindado para essa soldagem no início de 1944, os engenheiros se concentraram em automatizar as costuras mais extensas e carregadas mecanicamente.
Na planta nº 200 de Chelyabinsk, no processo de montagem do casco do tanque pesado IS-2, apenas 25% de todas as soldas puderam ser automatizadas. Em meados de 1944, Tankograd foi capaz de automatizar 18% de todos os 25% possíveis de soldas. O comprimento total das costuras soldadas ao longo do casco do tanque pesado IS-2 foi de 410 metros corridos, dos quais 80 metros corridos foram executados pelo método de soldagem automatizada.
Este resultado levou a economias significativas em recursos escassos e eletricidade. Foi possível liberar até 50 soldadores manuais qualificados (seus custos de mão de obra no valor de 15.400 homens-hora) e economizar 48.000 quilowatts-hora de eletricidade. Consumo reduzido de eletrodos (cerca de 20.000 kg, austenítico - 6.000 kg), oxigênio (em 1.440 metros cúbicos).
O tempo gasto na soldagem também foi reduzido significativamente. Por exemplo, soldar o fundo e a caixa da torre nas laterais com uma costura de dezesseis metros levou 9,5 horas-homem no modo manual e apenas 2. Uma costura semelhante em comprimento conectando o fundo às laterais do casco do tanque no modo automático necessária 3 horas-homem (no manual imediatamente 11, 4). Ao mesmo tempo, soldadores altamente qualificados poderiam ser substituídos por trabalhadores não qualificados em soldagem automática.
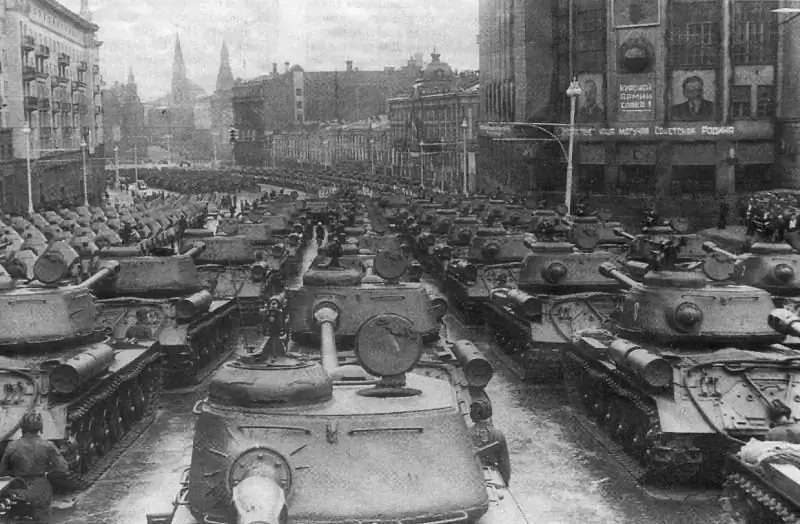
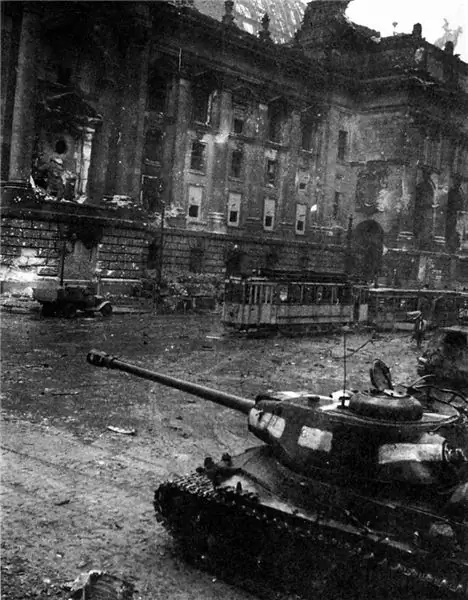
Ural SAGs
Pesquisador da indústria de tanques soviética, candidato de ciências históricas Zapariy Vasily Vladimirovich do Instituto de História e Arqueologia do Ramo Ural da Academia Russa de Ciências em uma de suas obras descreve em grande detalhe as unidades de soldagem automática usadas nos Urais para blindados produção de cascos.
O mais difundido era um fuzil de assalto do tipo "ACC" com cabeça de Bushtedt. Havia oito dessas instalações em Uralmash. A velocidade de alimentação do arame nesta máquina depende da tensão no arco. São necessárias 5 unidades, incluindo 3 motores elétricos cinemáticos e 1 motor-gerador.
Em meados de 1943, a máquina de solda SA-1000 foi projetada para as necessidades dos tanques pesados IS-2. Ou uma máquina de solda com capacidade de até 1000 A.
A fim de dominar a produção de cascos blindados para o novo tanque pesado IS-3 de Chelyabinsk, os engenheiros da fábrica em 1944 projetaram o aparelho "SG-2000". Esta máquina foi projetada para trabalhar com fios de solda de baixo carbono com diâmetro aumentado (6-8 mm) e encontrou sua aplicação na fabricação da torre IS-3. A instalação tinha um dispensador para a introdução de uma composição especial (várias ligas de ferro) na seção de solda para desoxidar (restaurar) o metal nela. No total, com base no princípio da autorregulação do arco de soldagem na UZTM, até 1945, foram criadas 9 instalações de autossoldagem de três tipos: "SA-1000", "SG-2000", "SAG" ("Soldagem automática cabeça").
Mais bonita do que a armadura alemã
O resultado de toda a história com a armadura de tanques pesados IS foi um desenvolvimento surpreendentemente rápido de uma receita de aço que ultrapassou a armadura alemã em suas propriedades táticas. O TsNII-48 recebeu um aço endurecível de 120 mm, cuja espessura, se necessário, poderia ser aumentada para 200 mm.
Esta se tornou a principal base para o desenvolvimento da família de tanques soviéticos pesados do pós-guerra.