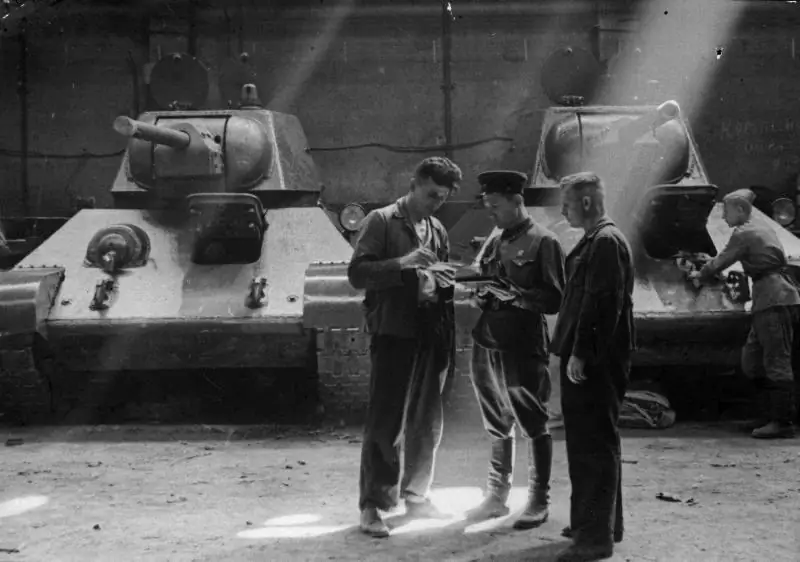
Todos para a guerra com um crack
O aço de blindagem 8C homogêneo, altamente sólido, que se tornou o principal para o tanque médio T-34, introduziu muitas dificuldades no processo de produção. Deve-se notar que essa blindagem sólida foi usada em tanques apenas na União Soviética durante toda a Segunda Guerra Mundial. E nisso, é claro, havia aspectos positivos e negativos. Nas partes anteriores do ciclo, já discutimos as numerosas rachaduras que acompanham a soldagem dos cascos e torres dos tanques médios soviéticos. Ao mesmo tempo, KV pesados e, em seguida, ISs foram privados disso: a armadura mais dúctil de dureza média tolerava tensões excessivas ao soldar peças com muito mais facilidade. Desde o início de 1942, os engenheiros do Armored Institute propuseram um conjunto de medidas para simplificar a produção de cascos blindados e modernizar a tecnologia de soldagem. Decidiu-se não soldar alguns nós: por exemplo, a fixação das estruturas traseira e frontal foi transferida para a rebitagem. Em muitos aspectos, foi um empréstimo após um estudo completo dos veículos blindados alemães.
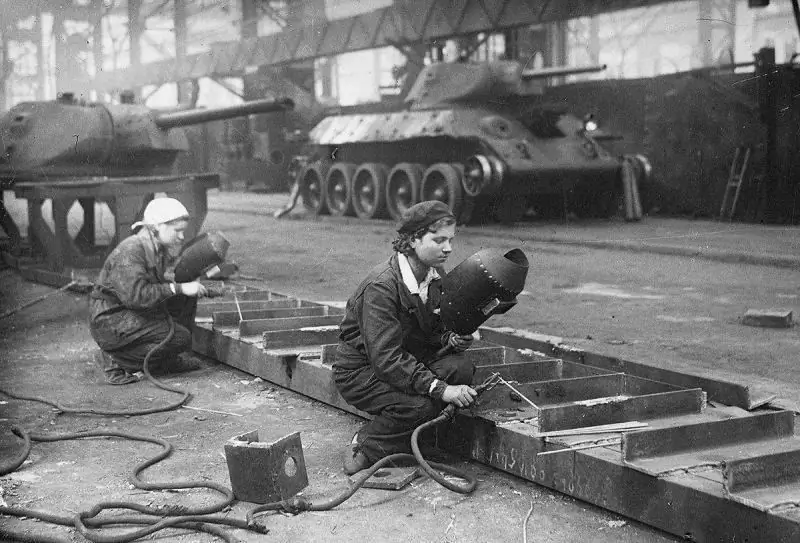
As partes frontal e lateral do tanque foram agora soldadas a pedido do TsNII-48 apenas com eletrodos de austenita, mais adequados para classes de metal ferroso de difícil soldagem. No total, agora até 10% (ou mais) de todos os eletrodos consumidos por um veículo blindado eram austenita. Se você se concentrar nos dados fornecidos no livro de Nikita Melnikov "Indústria de Tanques da URSS durante a Grande Guerra Patriótica", cerca de 400 eletrodos foram consumidos para um T-34-76, e 55 deles eram austenita. Entre os requisitos para o uso de tais eletrodos estava a proibição de sua operação em modos de alta corrente - até 320A. Exceder este indicador ameaçava com alto aquecimento da área de solda com subsequente deformação durante o resfriamento e formação de trincas. De notar que funções semelhantes às do "Instituto Blindado" doméstico na Alemanha foram desempenhadas pelo 6º Departamento da Direcção de Armamentos das Forças Terrestres. Era a ele que as fábricas de tanques deveriam submeter os métodos de soldagem de cascos e torres para aprovação por escrito. Os especialistas do 6º Departamento, por sua vez, verificaram os materiais apresentados quanto ao cumprimento das especificações provisórias para blindagem de soldagem T. L.4014, T. L.4028 e T. L.4032. Esses requisitos foram calculados para a soldagem de blindagem alemã com espessura de 16 a 80 mm. Conforme já mencionado no artigo "Soldagem de blindagem de tanque: experiência alemã", a soldagem automática não era usada na Alemanha. Isso, é claro, diminuiu seriamente a velocidade da indústria de tanques alemã, mas havia alguns problemas com máquinas de solda na União Soviética. Junto com a indiscutível alta qualidade da solda, a automação da soldagem exigia materiais de enchimento de alta qualidade e estrita aderência à tecnologia de trabalho. No entanto, este foi um preço inevitável a pagar pela introdução de um método de produção revolucionário, que teve um impacto tão significativo na qualidade e na velocidade da montagem do tanque.
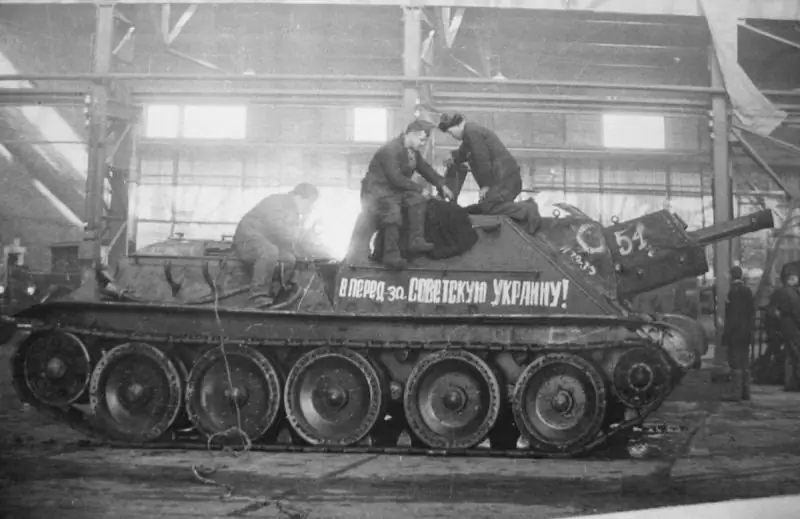
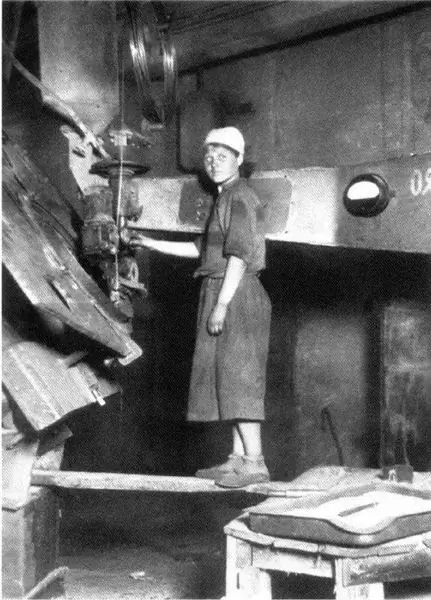
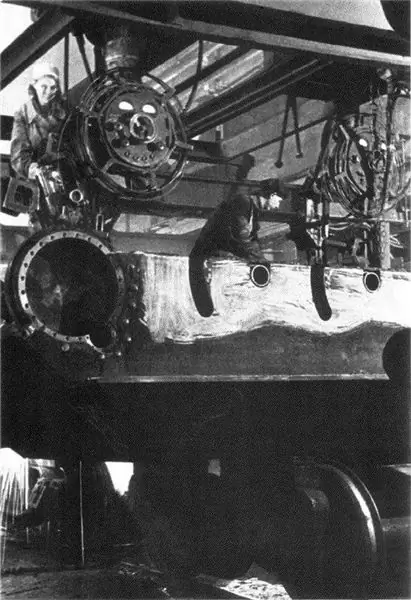
Se o eletrodo principal e o fio de adição revelassem estar excessivamente contaminados com enxofre, carbono e fósforo (ou, inversamente, faltasse manganês ou óxido de manganês), isso levava à formação de trincas diretamente na solda. Era importante preparar cuidadosamente os produtos a serem soldados sob fluxo. Os requisitos eram difíceis: as peças deveriam ter as dimensões corretas, sem violações de tolerâncias. Caso contrário, para a soldagem, a peça na rampa tinha que ser "puxada", criando assim graves tensões internas. E a simples não observância da força e da tensão da corrente de soldagem levava à imperfeição das costuras: porosidade, narinas e falta de penetração. Dado o baixo nível de qualificação dos trabalhadores com acesso às máquinas de solda, é fácil acreditar na possibilidade de tais defeitos. Todos os soldadores altamente qualificados estavam envolvidos na soldagem manual e não podiam influenciar a qualidade de soldagem das "máquinas de Paton". Embora eles estivessem envolvidos na correção de defeitos em máquinas de solda.
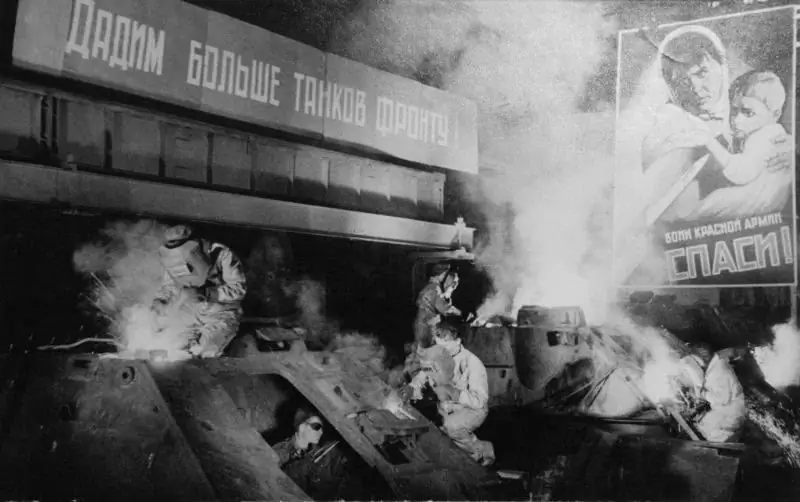
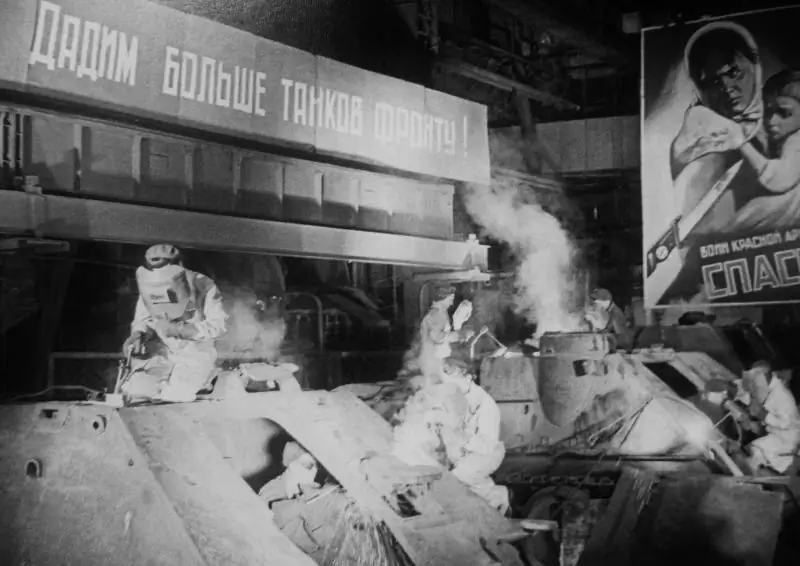
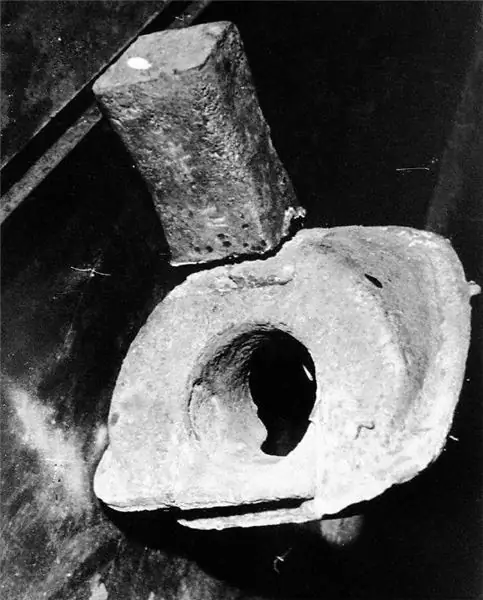
O aumento dramático na produtividade das fábricas de tanques levou a um problema inesperado em 1943. Acontece que o resto da produção nem sempre acompanhou a construção do tanque. As máquinas trabalhavam com desgaste, às vezes não havia amperímetros para controlar a força de corrente nas máquinas, faltavam eletrodos de soldagem de alta qualidade. Tudo isso causava "rajadas" periódicas de rachaduras entre os T-34s seriais. Para extinguir essas ondas de casamento teve que ser feito pelas forças operacionais de tecnólogos e engenheiros de fábrica do TsNII-48.
Revisão do design
A armadura dura e as rachaduras forçaram os engenheiros a mudar não apenas a tecnologia de soldagem automática, mas também a abordagem manual. Grandes soldagens e tensões térmicas, em particular, foram vivenciadas pela parte frontal superior, quando a proteção da metralhadora DT, ilhós, uma alça da escotilha do motorista, uma barra de proteção e outras ninharias foram soldadas nesta durante a linha de montagem. Em torno da proteção da metralhadora, que foi cuidadosamente escaldada, muitas vezes havia rachaduras de até 600 mm de comprimento! A soldadura era volumosa na zona do arco dos lados, onde eram fixados com poderosas costuras dupla-face com as placas frontais superiores e inferiores, bem como com braquetes de preguiça. Freqüentemente, a folga entre as peças nessas peças não correspondia às normativas e, portanto, era necessário fazer uma costura de solda particularmente maciça, deixando para trás sérias tensões internas. Era necessário reduzir a rigidez de alguns nós e diminuir a participação total da soldagem nas juntas, o que foi feito por especialistas em TsNII-48 no menor tempo possível. Em particular, o método de conectar as camisas do arco da roda à parte frontal do teto do casco foi alterado. Com a ajuda de uma faixa especial de "amortecimento" feita de aço macio, previamente soldada ao forro do para-lama, foi possível reduzir o nível de tensão final dentro da costura e ao redor da armadura. A seguir, descobrimos a "infraestrutura" mencionada na placa frontal do tanque. Agora, de acordo com as novas condições técnicas, era possível soldar os olhais, a proteção da metralhadora e as dobradiças da escotilha apenas com eletrodos de 5-6 mm em várias camadas: pelo menos quatro! De forma semelhante, as defensas foram conectadas ao teto, a placa frontal com as laterais, as defensas e o teto. Todo o resto foi cozido em 2-3 passagens com eletrodos de 7-10 mm.
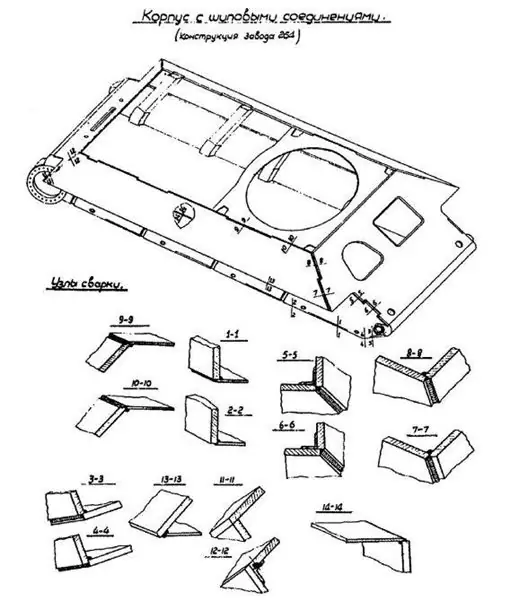
A tecnologia de união de peças do casco do tanque T-34 também foi alterada. Inicialmente, todas as conexões, exceto a interface do VLD e NLD, foram feitas em um trimestre conforme desenhos. Mas logo após o início da guerra, eles foram transformados em espinhos, mas isso também não se justificou - muitas rachaduras apareceram nos locais onde as costuras foram cortadas. A conexão de pico para blindagem de alta dureza não era totalmente apropriada também devido às fortes tensões de retração locais após a soldagem. O que era bom para a blindagem alemã de plástico não era adequado para os T-34 domésticos. Somente em 1943 no "tanque da vitória" surgiram as opções finais de articulação, que satisfizeram os especialistas do TsNII-48 - sobrepostas e costas com costas.
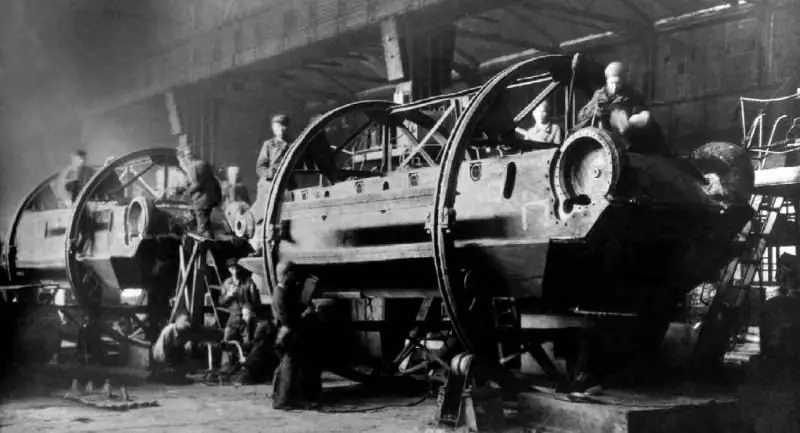
Os cascos dos pesados tanques soviéticos passaram pelo processo mais simples de otimizar as operações de soldagem. A conexão das placas de blindagem em um quarto no KV foi deixada inalterada, mas os cotovelos de reforço internos foram substituídos por soldas de filete internas. Já no meio da guerra, para tanques pesados, foram escolhidas as configurações mais ideais de placas de blindagem de acasalamento (primeiro com o bombardeio). Se o ângulo de conexão fosse próximo a 90 graus, então seria melhor usar o método "em um espinho" ou em um quarto, e em todas as outras variantes - em uma coluna vertebral ou em um dente. Como resultado desses estudos, uma forma peculiar da parte superior do conjunto de proa do tanque IS-2 nasceu em TsNII-48, quando, com uma espessura de 100-110 mm, a armadura fornecia proteção total contra Projéteis de 88-105 mm. Juntar as peças nesta construção sólida foi uma surpresa simples.