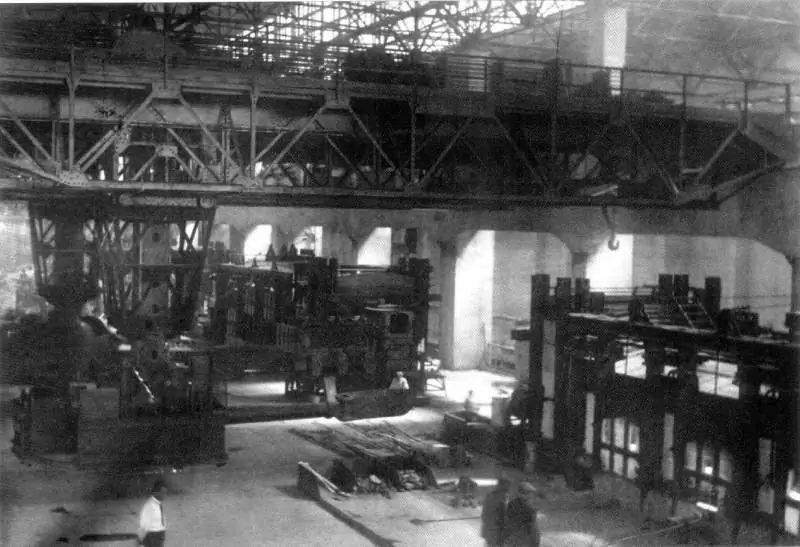
Recurso estratégico
É difícil superestimar a produção de aço de alta qualidade para o complexo militar-industrial em condições de guerra. Este é um dos fatores mais importantes para o sucesso dos exércitos no campo de batalha.
Como você sabe, os metalúrgicos de Krupp foram os primeiros a aprender como produzir aço de alta qualidade para armas.
Os alemães adotaram o processo de fabricação Thomas no final do século XIX. Esse método de fundição do aço possibilitou a remoção das impurezas de fósforo do minério, o que aumentou automaticamente a qualidade do produto. Armaduras de alta qualidade e aço para armas durante a Primeira Guerra Mundial frequentemente garantiam a superioridade dos alemães no campo de batalha.
Para organizar tal produção, novos materiais refratários foram necessários, que revestiram as superfícies internas dos fornos. Os alemães usaram os mais modernos refratários de magnesita para a época, resistindo a temperaturas de mais de 2.000 graus. Essas substâncias de maior refratariedade são baseadas em óxidos de magnésio com pequenas misturas de óxidos de alumínio.
No início do século 20, os países com tecnologias para a produção em massa de refratários de magnesita podiam se dar ao luxo de produzir armaduras e canos de armas de alta qualidade. Isso pode ser comparado a uma vantagem estratégica.
Mais baixos em termos de resistência ao fogo foram os chamados materiais altamente refratários que suportam temperaturas de 1750 a 1950 graus. Estes são os refratários de dolomita e de alta alumina. Materiais refratários de argila refratária, semi-ácidos, quartzo e dinas podem suportar temperaturas de 1610 a 1750 graus.
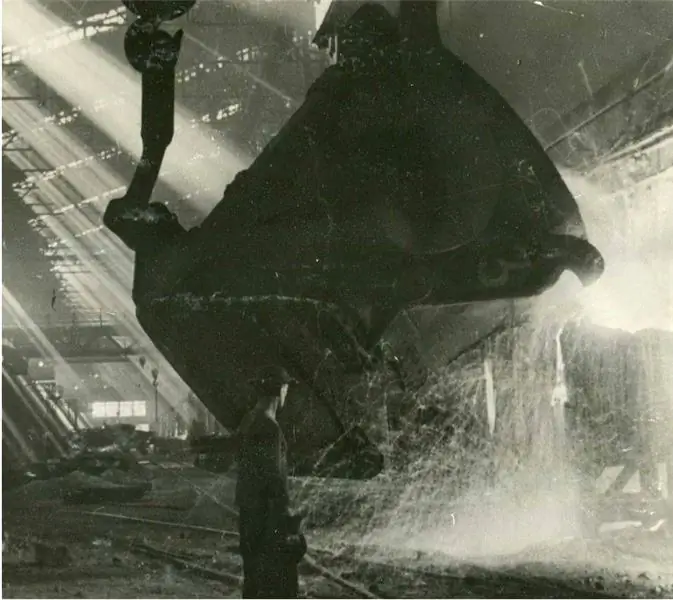
A propósito, tecnologias e locais para a produção de refratários de magnesita apareceram pela primeira vez na Rússia em 1900.
O tijolo refratário de magnesita Satka em 1905 foi premiado com uma medalha de ouro na Exposição Industrial Mundial em Liege. Foi produzido perto de Chelyabinsk, na cidade de Satka, onde um depósito único de magnesita foi localizado.
O mineral periclásio, do qual os refratários eram feitos na fábrica, era de alta qualidade e não precisava de enriquecimento adicional. Como resultado, o refratário de magnesita de Satka era superior aos seus equivalentes da Grécia e da Áustria.
Preenchendo a lacuna
Apesar do tijolo de magnesita de alta qualidade de Satka, até os anos 30, os principais refratários dos metalúrgicos soviéticos eram materiais dinas de argila. Naturalmente, obter uma alta temperatura para fundir aço para armas não funcionou - o revestimento interno dos fornos de lareira desmoronou e exigiu reparos extraordinários.
Não havia tijolos Satka suficientes e, no período pós-revolucionário, as principais tecnologias de produção foram perdidas.
Ao mesmo tempo, os europeus foram na frente - por exemplo, a magnesita austríaca Radex se distinguiu pela excelente resistência ao fogo.
A União Soviética comprou este material. Mas era impossível conseguir um análogo sem um segredo de produção. Esse problema foi abordado por um graduado da Universidade Técnica do Estado de Moscou. N. E. Bauman Alexey Petrovich Panarin. Na fábrica Magnet (anteriormente Satka Combine) em 1933, ele chefiou o Laboratório Central de Plantas. E cinco anos depois, ele lançou a produção em massa de refratários de periclase-cromita ou cromomagnesita para fornos de lareira.
Na Usina Metalúrgica Zlatoust e no Martelo e Foice de Moscou, o refratário Panarin substituiu o Dinas desatualizado.
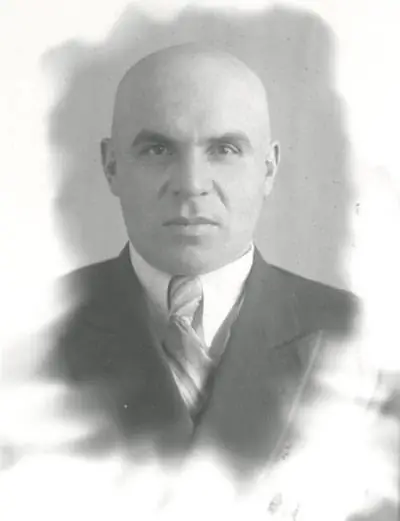
A tecnologia, que vinha sendo desenvolvida no laboratório da "Magnezit" há vários anos, consistia em uma composição e tamanho de partícula especiais.
Anteriormente, a fábrica produzia tijolos convencionais de cromo-magnesita, compostos por magnesita e minério de ferro cromo, na proporção de 50/50. O segredo revelado pelo grupo de Panarin foi o seguinte:
“Se o minério de cromita em grãos granulométricos grossos com um teor mínimo de frações inferior a 0,5 mm for adicionado a uma carga de magnesita comum, então, mesmo com uma adição de 10% desse minério, a estabilidade térmica do tijolo aumenta drasticamente.
À medida que aumenta a adição de minério de cromita de granulometria grossa, a estabilidade do tijolo cresce e atinge o máximo em uma determinada proporção de componentes.”
A cromita do novo refratário foi retirada na mina de Saranovskoye e o periclásio continuou a ser extraído em Satka.
Para efeito de comparação, um tijolo de magnesita "pré-revolucionário" comum resistiu a temperaturas 5 a 6 vezes menos do que a novidade da Panarin.
Na usina de fundição de cobre de Kirovograd, o refratário de magnesita e cromo no telhado de um forno reverberatório resistiu a temperaturas de até 1.550 graus por 151 dias. Anteriormente, os refratários em tais fornos tinham que ser trocados a cada 20-30 dias.
Em 1941, a produção de refratários em grande escala foi dominada, o que tornou possível usar os materiais em grandes fornos de siderurgia em temperaturas de até 1.800 graus. Uma contribuição importante para isso foi feita pelo diretor técnico da "Magnezit" Alexander Frenkel, que desenvolveu um novo método de fixação do material refratário nos tetos dos fornos.
Refratários para a vitória
No final de 1941, os metalúrgicos de Magnitka realizaram o que antes era impensável - pela primeira vez na história, eles dominaram a fundição de aço blindado para tanques T-34 nos principais fornos pesados de lareira.
O principal fornecedor de refratários para um processo tão importante foi a Satka "Magnezit". Não é preciso falar das dificuldades do tempo de guerra, quando um terço dos operários foi chamado para o front e o Estado exigiu que o plano fosse superado. No entanto, a fábrica estava fazendo seu trabalho, e a Panarin em 1943
"Para dominar a produção de produtos altamente refratários a partir de matérias-primas locais para metalurgia ferrosa"
foi agraciado com o Prêmio Stalin.
Em 1944, este metalúrgico-pesquisador desenvolverá uma tecnologia para a produção de pó de magnesita de alta qualidade "Extra". Este produto semi-acabado foi usado para preparar um refratário prensado usado na produção especialmente importante de aço blindado em fornos elétricos. O limite de temperatura para esses refratários atingiu 2.000 graus.
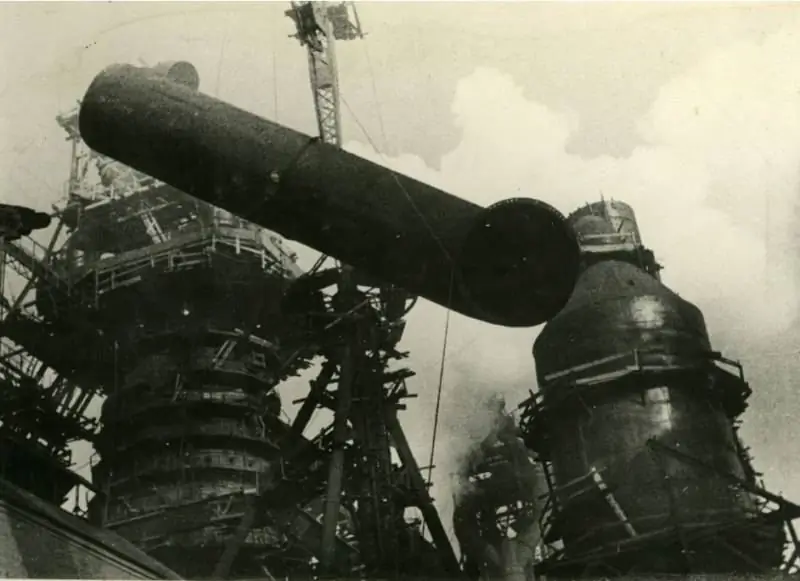
Mas não se deve presumir que o exemplo de uma fábrica Magnezit de sucesso geral se estendeu a toda a indústria de refratários da União Soviética.
Uma situação particularmente difícil desenvolveu-se nos Urais, onde praticamente todos os tanques do país foram evacuados em 1941-1942.
As plantas metalúrgicas Magnitogorsk e Novotagilsk foram reorientadas para a produção de blindados, fornecendo produtos para Sverdlovsk Uralmash, Chelyabinsk "Tankograd" e planta de tanques Nizhny Tagil nº 183. Ao mesmo tempo, as plantas metalúrgicas tinham sua própria produção de refratários a partir de matérias-primas locais.
Por exemplo, em Magnitka, a fábrica de dinas-chamotte produzia 65-70 mil toneladas de tijolos por ano. Isso não era suficiente nem mesmo para suas próprias necessidades, sem falar no abastecimento de outras empresas.
As primeiras dificuldades surgiram quando as fábricas de tanques começaram a construir seus próprios aquecedores e fornos térmicos. A metalurgia dos Urais mal tinha refratários suficientes e, então, a produção de cascos das fábricas de tanques exigia materiais de alta qualidade para o revestimento dos fornos.
Não se falava de nenhum refratário de cromomagnesita aqui - esse material era escasso e até exportado em troca da American Lend-Lease. Pelo menos isso é mencionado em várias fontes. Os historiadores dos Urais escrevem que a cara cromomagnesita de Panarin poderia ir para o exterior em troca de ferroligas escassas para blindagem de tanques. Mas não há evidência direta disso ainda.
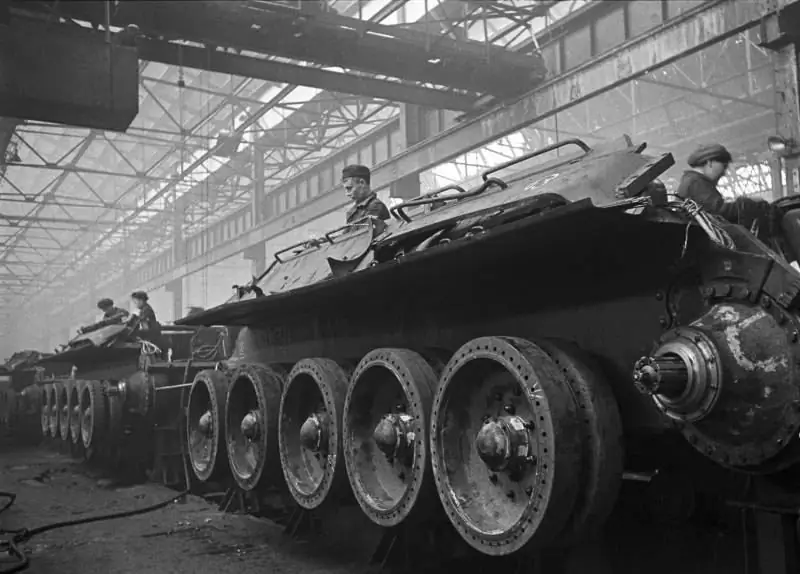
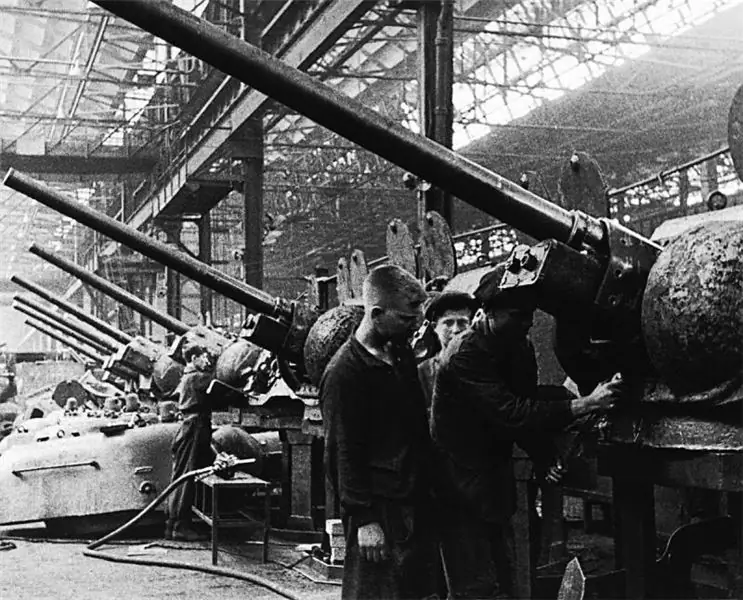
As fábricas de tanques dependiam principalmente de material refratário Dinas produzido pela planta de Pervouralsk. Mas, em primeiro lugar, ela era produzida apenas 12 mil toneladas por mês e, em segundo lugar, os metalúrgicos ficavam com a parte do leão.
A expansão da produção na fábrica de Pervouralsk foi muito lenta. E em meados de 1942, surgiram apenas 4 novos fornos. O resto não estava pronto ou geralmente existia apenas em projetos.
Os refratários para fornos de lareira de fábricas de tanques geralmente eram de baixa qualidade, não estavam cheios e na hora errada. Apenas para o reparo dos fornos Uralmash no quarto trimestre de 1942, foram necessárias 1.035 toneladas de tijolos resistentes ao fogo, e apenas cerca de 827 toneladas foram recebidas.
Em 1943, a oficina de fogo aberto de Uralmash, em geral, quase parou devido à falta de refratários para reparo.
A qualidade dos refratários fornecidos durante a guerra deixou muito a desejar. Se, em condições normais, o tijolo de dinas da fornalha de lareira pudesse resistir a 400 calores, então em tempo de guerra não ultrapassava 135 calores. E em março de 1943, esse parâmetro caiu para 30-40 baterias.
Esta situação demonstra claramente como a falta de um recurso (neste caso, refratário) pode retardar seriamente o trabalho de toda a indústria de defesa. Como escreve o candidato às ciências históricas Nikita Melnikov em suas obras, em março de 1943, três fornos de lareira de Uralmash ainda pararam e realizaram um ciclo completo de reparos. Foram necessários 2346 toneladas de dinas, 580 toneladas de chamotte e 86 toneladas de magnesita escassa.
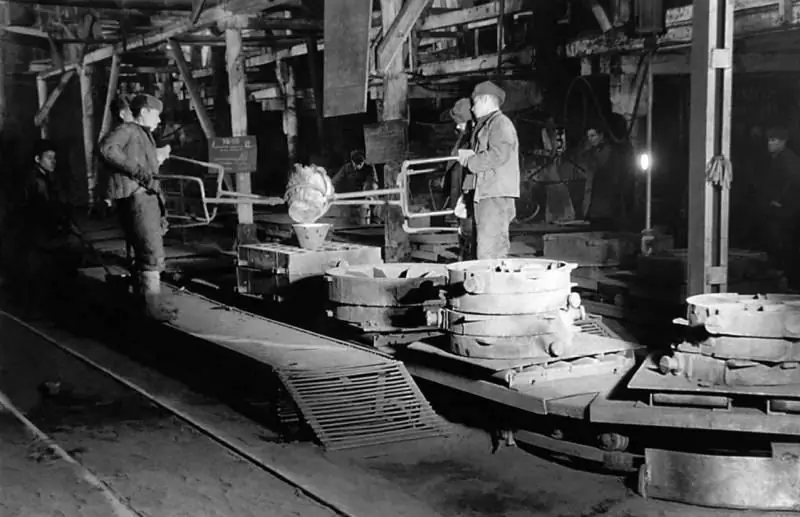
Em meados de 1942, na planta de tanques nº 183, a situação evoluía de maneira semelhante - a produção de aço ficava atrás da montagem mecânica. E tivemos que "importar" os cascos do T-34 de Uralmash.
Um dos motivos era a falta de refratários para o reparo dos fornos de sola aberta, que na primavera de 1942 funcionavam no limite. Como resultado, apenas 2 dos 6 fornos de lareira aberta estavam em operação no outono. Os volumes de fundição foram restaurados apenas na segunda metade de 1943.
A situação dos refratários na estrutura do complexo de defesa soviético durante a Grande Guerra Patriótica ilustra claramente a complexidade da situação na retaguarda do país.
Uma escassez crônica de, em geral, não o produto mais de alta tecnologia afetou diretamente o ritmo de produção de veículos blindados.