O patriotismo da elite industrial soviética foi combinado com a responsabilidade conjunta pelo resultado final
A interação interindustrial em todos os momentos - tanto no Império Russo, quanto na URSS e hoje - não pertencia aos pontos fortes da indústria nacional. Em contraste com a Alemanha ou os Estados Unidos, onde as obrigações contratuais tinham e têm uma força imutável e quase sagrada.
Considere, por exemplo, a relação entre metalúrgicos russos e fabricantes de máquinas. Na segunda metade do século 19, novas fábricas de engenharia de transporte e estaleiros navais não recebiam a quantidade necessária de metais industriais dos mineiros dos Urais. Este último considerou não lucrativo fazer muitos produtos laminados relativamente baratos, uma vez que o mesmo lucro era fornecido por um volume muito menor de ferro para telhados caro. O metal que faltava para os eixos dos carros, eixos do motor e revestimento do navio teve que ser comprado no exterior. Somente no final do século, o problema foi resolvido pelas usinas metalúrgicas do sul da Rússia, fundadas por industriais belgas ou franceses. Nos Urais, os franceses também construíram uma fábrica - Chusovskaya.
Parece que nos tempos soviéticos, tais caprichos estavam fora de questão. Além disso, as siderúrgicas construídas na década de 30 abasteciam o país com o metal como um todo. No entanto, cada vez que os fabricantes de máquinas solicitavam novos tipos complexos de produtos laminados, os metalúrgicos os dominavam por anos ou mesmo décadas.
Feudalismo departamental
Vamos voltar para a história de Uralvagonzavod. Já em seus primeiros projetos, foi planejado o uso de rodas de aço laminado maciço sob os carros de quatro eixos à medida que a capacidade do projeto atingisse sua capacidade projetada, cujo fornecedor foi planejado para a fábrica metalúrgica Novo-Tagil, nas proximidades. Porém, este último estava sendo construído pelo departamento de metalurgia, e postergou a construção do laminador de rodas para 1938-1942, e não em primeiro lugar. Como resultado, o caso não começou antes da guerra. E depois da guerra, o aluguel de rodas não interessou muito aos metalúrgicos. Resultado: até meados dos anos 50, os carros Tagil saíam de fábrica com rodas de ferro fundido de curta duração em vez de rodas de aço. Isso trouxe enormes prejuízos aos ferroviários, mas não havia escolha: ou esses carros ou nenhum.
O mesmo aconteceu com a introdução dos aços de baixa liga na construção de carruagens. Eles prometeram uma redução notável no peso morto do material rodante, mantendo todas as características de desempenho. Os projetistas de Uralvagonzavod começaram a projetar carros feitos de metal de baixa liga no final dos anos 30, mas sua produção em série começou apenas na segunda metade dos anos 50, uma vez que os metalúrgicos não forneciam produtos laminados ou ferroligas adequados para fundir peças.
É preciso dizer que o vírus do feudalismo departamental afetou os próprios construtores de máquinas. No verão de 1937, aconteceu uma história interessante que caracterizou as relações interagências da época. A Direcção-Geral das Empresas Metalúrgicas enviou à Uralvagonzavod uma encomenda de cinco mil toneladas de blanks para o recém-inaugurado moinho de ligaduras da Fábrica Novo-Tagil. A Diretoria Principal de Engenharia de Transporte ficou indignada com a invasão de uma empresa subordinada. Vice-Chefe da Diretoria Principal G. G. Em 11 de julho, Aleksandrov enviou uma carta ao GUMP e ao Uralvagonzavod com a seguinte declaração: “Estamos extremamente surpresos que a solução de uma questão tão importante como a organização da produção de uma faixa em branco em Uralvagonzavod tenha sido realizada sem a nossa participação, e ainda mais - não nos foi nem enviada uma cópia do traje enviado para Uralvagonzavod … Peço que estabeleça um procedimento firme para a emissão de espaços em branco para nossas fábricas somente por acordo conosco e por meio da Glavtransmash."
Como resultado, os metalúrgicos viram negado o aço da atadura, supostamente devido à impossibilidade técnica de lançar lingotes de alta qualidade na oficina a céu aberto de Uralvagonzavod. Enquanto isso, já em 1936, uma peça bruta axial foi lançada aqui, e em 1937 - lingotes para laminação de folhas. Portanto, os lingotes para o moinho de cobertura, localizado a poucos quilômetros de UVZ, tiveram que ser transportados das fábricas de Vyksa e Kuznetsk. Além disso, sua qualidade deixava muito a desejar e os volumes de suprimentos eram insuficientes.
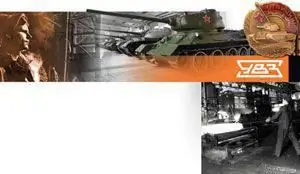
Em 1938, a história se repetiu. O principal consumidor dos lingotes UVZ era a Usina de Artilharia Molotov (ou seja, Perm), que recebia um lote de blanks no final do ano. E apenas um pequeno número deles foi à loja de curativos, que novamente teve que importar o metal que faltava por dois ou dois mil e quinhentos quilômetros. Os interesses da indústria na distribuição do aço Uralvagonzavodsk prevaleceram claramente.
Doenças departamentais também não pouparam a indústria de defesa. Numerosas publicações sobre a história da construção de tanques soviéticos estão completamente repletas de exemplos de como a construção de protótipos ou a implantação da produção em massa foi atrasada devido à não entrega de metal, especialmente blindados.
E ainda hoje o interesse próprio setorial não foi a lugar nenhum, apenas mudou de forma. Os pedidos de novos formatos de produtos laminados são simplesmente eliminados com preços exorbitantes. Não há necessidade de falar sobre uma política coordenada. Após o colapso da taxa de câmbio do rublo na virada de 2014-2015, as empresas metalúrgicas aumentaram os preços do material rodante em 30-60 por cento. E eles imediatamente começaram a reclamar dos fabricantes de máquinas para os equipamentos que haviam subido de preço - afinal, as máquinas são produzidas na Rússia e não estão vinculadas à taxa de câmbio do dólar.
Parece que em nosso país só existe uma cura para os problemas intersetoriais: a criação de sistemas integrados verticalmente, onde o minério extraído por nossas próprias forças é transformado primeiro em metal e depois em máquinas acabadas.
Unidade de tempo de guerra
No entanto, há um curto período em nossa história em que os interesses da indústria ficaram em segundo plano. Estamos falando sobre a Grande Guerra Patriótica. O indubitável patriotismo da elite industrial soviética da época combinava-se com a responsabilidade conjunta de todos os envolvidos na produção de defesa pelo resultado final. Ou seja, o diretor da laminação blindada era responsável não tanto pelo volume de aço fundido e laminado, mas pela quantidade de tanques construídos.
O principal passo nessa direção foi dado pelo diretor da NII-48 A. S. Zavyalov. Nos primeiros dias da guerra, ele dirigiu-se ao governo com a proposta de instruir o instituto a introduzir tecnologias para a produção de aços especiais e estruturas blindadas em empresas do leste do país, as primeiras envolvidas na fabricação de blindados veículos. No início de julho, equipes de especialistas do NII-48 lideraram a reestruturação tecnológica de 14 grandes empresas. Entre eles estavam as plantas metalúrgicas Magnitogorsk e Kuznetsk, as plantas metalúrgicas Novo-Tagil e Chusovka, a planta de construção de máquinas pesadas de Ural, a Gorky Krasnoye Sormovo, a planta de trator de Stalingrado, o outubro vermelho de Stalingrado e o nº 264. Assim, Zavyalov violou o tabu pré-guerra: a lista incluía empresas de comissariados de três pessoas.
O patriotismo e a supressão compulsória do egoísmo departamental forneceram à metalurgia soviética taxas sem precedentes de desenvolvimento de produtos de defesa, nem no pré-guerra nem no pós-guerra. Em questão de meses, no leste do país (principalmente nos Urais), organizou-se a produção de ferromanganês, ferrossilício, ferrocromo, ferrovanádio e outras ligas, sem os quais é impossível obter aços blindados. Após a perda das regiões ocidentais, Chelyabinsk permaneceu como a única usina de ferroligas na URSS. Nele, em pouco tempo, a fundição foi aumentada em duas vezes e meia. Foram produzidos 25 tipos de produtos, mas a maioria era de vários tipos de ferrocromo. A fundição de ferromanganês foi estabelecida em altos-fornos, e não apenas em altos-fornos antigos de baixa tonelagem das fábricas de Nizhniy Tagil e Kushvinsky, mas também em um grande forno moderno da Combine Magnitogorsk. Ao contrário de todas as idéias pré-guerra, o ferrocromo foi fundido na segunda metade de 1941 em seus altos-fornos por metalúrgicos das fábricas de Nizhniy Tagil e Serov, e cientistas da filial de Ural da Academia de Ciências da URSS forneceram grande ajuda na criação de um novo tecnologia. Mais tarde, a fundição de ferrossilício foi dominada nos altos-fornos de Serov.
Não havia acampamentos blindados nos Urais ou na Sibéria Ocidental antes da guerra, eles tiveram que ser transferidos às pressas das empresas que estavam na zona de combate.
No verão de 1941, o equipamento evacuado ainda estava em trânsito. E então o mecânico-chefe do Magnitogorsk Combine N. A. Ryzhenko sugeriu enrolar a armadura em um moinho de flores. Apesar do grande risco, a ideia foi concretizada. E em outubro, um acampamento blindado, retirado da fábrica de Mariupol, entrou em serviço. Foi montado em apenas 54 dias. De acordo com os padrões do pré-guerra, isso levou um ano.
A fábrica Novo-Tagil recebeu o acampamento de Leningrado. Os preparativos para sua internação começaram em julho, inicialmente presumiu-se que seria montado no local da bandagem. O campo de bandagem foi desmontado, mas descobriu-se que o estoque antigo não era suficiente para instalar o campo blindado e teve que ser colocado em outro lugar. A guerra obrigou a fazer o que era considerado impossível até recentemente: apenas um ano atrás, as tentativas de realizar a construção industrial por um método integrado de "alta velocidade" em Nizhny Tagil tiveram, na melhor das hipóteses, um sucesso parcial, e no verão de 1941, no máximo. a operação de construção complexa foi quase perfeita. Em 10 de setembro, a primeira chapa de aço Tagil foi laminada um mês antes do planejado. No total, até o final do ano, 13.650 toneladas de chapas de metal foram obtidas, incluindo cerca de 60 por cento de blindagem (a usina foi testada em aço carbono, e em outubro-dezembro, aço carbono foi laminado com escassez de lingotes de blindagem). Como resultado, já em janeiro de 1942, a produção mensal de placas de blindagem nas fábricas dos Urais ultrapassava seis meses em toda a União Soviética antes da guerra.
Eventos nada menos surpreendentes aconteceram em outras empresas pouco conhecidas. Durante a guerra, a Usina Metalúrgica Zlatoust era inferior à Combine Magnitogorsk em termos de volume de fundição e aço laminado, mas superava significativamente em seu mix de produtos - cerca de 300 graus de liga e aço carbono foram produzidos aqui. Sem os suprimentos de Zlatoust, a produção de muitos tipos de armas, principalmente motores de tanques, teria parado.
As antigas fábricas dos Urais provaram ser indispensáveis na produção de pequenos lotes de aço especialmente de alta qualidade. Por exemplo, o metal da Serov Metallurgical, o principal fabricante de produtos laminados calibrados, foi investido em todos os tanques soviéticos. A planta de Nizhnesalda mudou para níquel, ferro e fundição de aço. Essa lista pode ser continuada indefinidamente - durante os anos de guerra, onde quer que houvesse pelo menos uma cúpula, metal para armas era derretido.
Existe uma curiosa história com fluxos para soldagem automática. Antes e no início da guerra, foram fundidos numa das empresas do Donbass, após a qual o abastecimento centralizado cessou por completo. No final de 1941, funcionários do Instituto de Soldagem Elétrica da Academia de Ciências da SSR Ucraniana começaram a procurar materiais substitutos disponíveis nos Urais em condições mais ou menos utilizáveis. E eles os encontraram - na forma de escórias de alto-forno da planta metalúrgica Ashinskiy. Apenas pequenas melhorias eram necessárias: os altos-fornos enriqueciam suas escórias com manganês e, assim, as transformavam em um fundente totalmente adequado. O equipamento necessário para o teste foi trazido de Nizhny Tagil diretamente para Asha.
Exemplos de cooperação local entre tanques e plantas metalúrgicas são muito indicativos. Antes do lançamento de suas próprias instalações, o tratamento térmico de partes do tanque da Planta de Tanques Ural No. 183 foi realizado na Planta Metalúrgica de Nizhniy Tagil.
O trabalho bem-sucedido dos trabalhadores da fundição da UTZ foi muito facilitado pela assistência da fábrica de argila refratária Nizhniy Tagil, que estabeleceu a produção de plugues de pederneira refratários de alta qualidade. Isso tornou possível realizar a fundição sem problemas de fundidos de aço de armadura pesada para fundição moldada.
Em 1942-1945, os fornos de sola aberta da UTZ operavam principalmente com forno de coque e gás de alto-forno das usinas de metalúrgica Novo-Tagil e de coque Nizhniy Tagil. O gasoduto está em operação desde fevereiro de 1942. A própria estação de geração de gás da planta nº 183 supria não mais do que 40% das necessidades.
Às vezes, um simples conselho bastava para resolver um problema. As informações de metalúrgicos locais sobre uma pequena mina de manganês desenvolvida na década de 1870 ajudaram a sobreviver várias semanas antes do início das entregas de ferromanganês sem interromper a fundição de rastros de tanques.
Outro exemplo: à medida que a produção de aço blindado aumentava, a oficina de lareira não conseguia mais acompanhar a fundição do metal para as cabeças das bombas aéreas. Não foi possível obtê-lo de fora. O diretor Yu. E. Maksarev relembrou o curso de eventos posteriores em suas memórias: “Quando eu estava em uma das reuniões no comitê da cidade, encontrei o diretor da antiga, ainda fábrica de Demidov e pedi para tirar de mim o elenco de as cabeças das bombas. Ele disse: Não posso ajudar com aço, mas com conselhos ajudarei. E quando cheguei na planta dele, ele me mostrou um conversor Bessemer de uma tonelada e meia com sopro médio. Ele me deu os desenhos e disse que sabe que temos uma boa fundição mecanizada de ferro e que seus conversores vão soldar”. Foi assim que surgiu o pedido da fábrica de 8 de setembro de 1942 na organização na oficina de rodas Griffin da seção Bessemer de três pequenos conversores (uma tonelada e meia de metal cada). Em 25 de setembro, o projeto foi elaborado pelo departamento de design e tecnologia da gestão de construção de capital, os especialistas do departamento de mecânica-chefe soldaram rapidamente conversores e caldeiras - tanques de armazenamento de ferro líquido. O teste de funcionamento do departamento de Bessemer e o lançamento de um lote experimental de cinco nomes de peças ocorreram na virada de outubro para novembro de 1942. A produção em série começou no final de novembro.
No final do tópico: a cooperação de metalúrgicos e construtores de tanques em tempo de guerra atuou em ambas as direções. Os instaladores da Usina Tanque Ural participaram do comissionamento de várias novas unidades da Usina Metalúrgica Novo-Tagil. Em maio de 1944, um número significativo de placas de revestimento para o reparo do alto-forno foi fabricado na fundição da torre blindada.
Mas o principal assistente dos metalúrgicos era, é claro, a fábrica de máquinas pesadas de Ural. Os livros de encomendas da UZTM para 1942-1945 estão literalmente repletos de documentos sobre a produção de peças sobressalentes e dispositivos para fins metalúrgicos - tanto para as necessidades da indústria de tanques como para as empresas do Comissariado do Povo da Metalurgia Ferrosa. No outono de 1942, uma divisão especial para a produção de equipamentos para plantas metalúrgicas foi oficialmente restaurada na UZTM. Recebia o código "Divisão 15" e estava subordinado ao vice-diretor de lojas de compras e produção de cascos.
Sucesso na interseção de setores
A cooperação de metalúrgicos e construtores de tanques levou à criação de uma série de tecnologias que, sem exagero, podem ser chamadas de verdadeiras descobertas científicas e técnicas.
Tendo derretido e enrolado aço blindado em folhas, os metalúrgicos transferiram seus produtos para a produção de cascos blindados. Aqui, o metal foi cortado de acordo com o modelo nas partes correspondentes. Na produção do "trinta e quatro", especialmente, muitos problemas foram causados por duas partes do casco: as defensas (o lado inclinado da lateral) e a placa lateral vertical. Ambos eram longos, mesmo em tiras largas com cortes oblíquos nas bordas.
A ideia naturalmente surgiu para enrolar uma tira de medição igual em largura às peças acabadas. Foi formulado pela primeira vez pelos carros blindados da fábrica de Mariupol no verão de 1941. Para a laminação experimental, escolhemos uma laminação de placas em Zaporizhstal, para onde foram enviados dois escalões de lingotes de blindagem. Mas então eles não tiveram tempo para começar a trabalhar: o avanço das tropas alemãs capturou os escalões e a própria Zaporozhye.
Na virada de 1941 para 1942, durante a evacuação e o desenvolvimento da produção de blindados nas novas fábricas, não havia tarja suficiente. No entanto, em maio de 1942, o Comissariado do Povo de Metalurgia Ferrosa recebeu novamente uma ordem para alugá-lo para tanques T-34 e KV. A tarefa acabou sendo difícil: as tolerâncias em largura não deveriam exceder -2 / + 5 milímetros, a forma crescente (curva) para o comprimento total da peça era de 5 milímetros. Trincas, pores do sol e delaminação não foram permitidos nas bordas para que a soldagem pudesse ser realizada sem usinagem ou corte à chama.
O trabalho experimental começou simultaneamente nas oficinas de laminação das plantas metalúrgicas Magnitogorsk e Kuznetsk, a princípio sem nenhuma realização particular. O aluguel de peças para os tanques KV foi logo abandonado, mas o T-34 finalmente obteve sucesso. A equipe de autores composta pelo chefe do departamento metalúrgico do NII-48 G. A. Vinogradov, o engenheiro-chefe da KMK L. E. Vaisberg e o engenheiro da mesma planta S. E. está "900" da ferrovia e da usina estrutural é um completamente novo método de rolar "na borda". Em janeiro de 1943, foram emitidas 280 tiras, em fevereiro - 486, em março - 1636 peças. Em abril, após todos os testes exigidos, iniciou-se o desenvolvimento da produção bruta de faixas de medição para as camisas dos arcos das rodas dos tanques T-34. Inicialmente, foram fornecidos para a UZTM e a Ural Tank Plant, e depois para outras fábricas - fabricantes de tanques T-34. A sucata, que originalmente era de 9,2%, caiu para 2,5% em outubro de 1943, e as tiras abaixo do padrão foram usadas para fazer peças menores.
Uma avaliação completa e precisa da nova tecnologia é fornecida pelo relatório correspondente do TsNII-48 datado de 25 de dezembro de 1943: "Um método fundamentalmente novo de rolar uma faixa blindada larga" na borda "foi desenvolvido, testado e introduzido na produção bruta, o que até recentemente era considerado inviável na URSS e no exterior. A obtenção de uma faixa calibrada (medida) com a largura da parte acabada do casco blindado do tanque T-34 possibilitou que as fábricas da NKTP adotassem uma nova tecnologia de alto desempenho para a fabricação de peças blindadas sem corte de arestas longitudinais. Graças à aplicação do novo método a uma das principais partes blindadas do tanque T-34 (pára-lamas), uma economia de tempo muito significativa (cerca de 36%) foi alcançada ao cortá-los. Atingiu economia de aço blindado 8C de até 15 por cento e economia de oxigênio de 15.000 cbm por 1000 cascos”.
No final de 1943, o rolamento de uma faixa de medição foi dominado para outra parte do casco do T-34 - a parte vertical da lateral. Resta acrescentar que os autores desta invenção receberam o Prêmio Stalin de 1943.
No mesmo 1943, por esforços conjuntos do laboratório do Instituto Ucraniano de Metais (chefiado por PA Aleksandrov) e trabalhadores da Ceifeira-debulhadora Metalúrgica de Kuznetsk e da Planta do Tanque de Ural, um perfil laminado periódico especial foi desenvolvido e dominado na produção para a aquisição de massa e partes críticas dos "trinta e quatro" - eixos balanceador. O primeiro lote experimental de um perfil periódico foi recebido na KMK em dezembro, no início de 1944 a produção seriada. Em outubro, a planta de tanques de Ural mudou completamente para a fabricação de eixos balanceadores de um novo blank, no final do ano a UZTM se juntou a ela. Como resultado, a produtividade dos martelos de forjamento aumentou 63 por cento e o número de quebras de peças diminuiu.
O sucesso do trabalho dos construtores de tanques foi muito facilitado pelo material rodante do laminador da Usina Metalúrgica Novo-Tagil. A partir da primavera de 1942, eles forneceram correias de ombro laminadas com tolerâncias de usinagem reduzidas; em 1943, as tolerâncias foram reduzidas novamente. Em combinação com a nova ferramenta de corte, isso tornou possível realizar uma decapagem demorada das alças de ombro estritamente dentro do cronograma e sem muito esforço. Um caso raro: o Comissário do Povo da Indústria de Tanques V. A. Malyshev, em seu despacho de 28 de setembro de 1943, considerou necessário expressar um agradecimento especial aos metalúrgicos de Tagil.
E, finalmente, o último exemplo: em 1943, os aros dos tanques de suporte T-34, primeiro na fábrica de Chelyabinsk Kirov, e depois em outras empresas, começaram a ser feitos de produtos laminados perfilados especiais. Esse sucesso também foi observado na ordem de V. A. Malyshev.
Resta acrescentar que os especialistas da empresa americana "Chrysler", tendo estudado o tanque T-34-85 capturado na Coréia, notaram especialmente a perfeição das placas de aço com as quais o veículo de combate foi feito. E também o fato de que muitas vezes superavam os produtos das empresas metalúrgicas dos Estados Unidos.