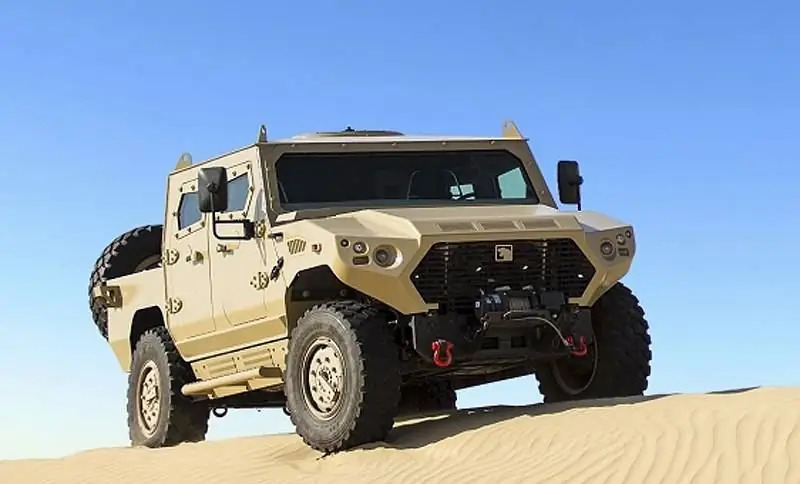
A armadura é milhões de anos mais velha que a humanidade e foi desenvolvida principalmente para proteger contra mandíbulas e garras. É possível que crocodilos e tartarugas possam inspirar parcialmente os humanos a criar elementos de proteção. Todas as armas de energia cinética, seja uma clava pré-histórica ou um projétil perfurante, são projetadas para concentrar uma grande força em uma pequena área, sua tarefa é penetrar no alvo e infligir o máximo de dano nele. Consequentemente, o trabalho da armadura é evitar isso desviando ou destruindo os meios de ataque e / ou dispersando a energia de impacto em uma área tão grande quanto possível, a fim de minimizar qualquer dano à mão de obra, sistemas de transporte e estruturas que protege.
A armadura moderna normalmente consiste em uma camada externa dura para parar, desviar ou destruir o projétil, uma camada intermediária com um "trabalho para quebrar" muito alto e uma camada interna viscosa para evitar rachaduras e detritos.
Aço
O aço, que se tornou o primeiro material amplamente utilizado na criação de veículos blindados, continua em demanda, apesar do surgimento de blindagens à base de ligas leves de alumínio e titânio, cerâmicas, compósitos com matriz polimérica, reforçados com fibras de vidro, aramida e polietileno de ultra-alto peso molecular, bem como materiais compósitos com matriz metálica.
Muitas siderúrgicas, incluindo SSAB, continuam a desenvolver aços de alta resistência para uma variedade de aplicações críticas de peso, como revestimento adicional. Aço blindado ARM OX 600T, disponível em espessuras de 4-20 mm, está disponível com uma dureza garantida de 570 a 640 unidades HBW (abreviatura de Dureza, Brinell, Wolfram; um teste em que uma bola de tungstênio de diâmetro padrão é pressionada em uma amostra de material com uma força conhecida, então o diâmetro do recesso formado é medido; então, esses parâmetros são substituídos na fórmula, o que permite obter o número de unidades de dureza).
SSAB também enfatiza a importância de atingir o equilíbrio certo entre dureza e tenacidade para proteção contra penetração e ruptura. Como todos os aços, o ARMOX 600T é composto de ferro, carbono e vários outros componentes de liga, incluindo silício, manganês, fósforo, enxofre, cromo, níquel, molibdênio e boro.
Existem restrições nas técnicas de fabricação utilizadas, principalmente no que diz respeito à temperatura. Este aço não se destina a tratamento térmico adicional; se aquecido acima de 170 ° C após a entrega, a SSAB não pode garantir suas propriedades. As empresas que conseguem contornar esse tipo de restrição provavelmente atrairão o escrutínio de fabricantes de veículos blindados.
Outra empresa sueca, a Deform, oferece peças moldadas a quente em aço blindado à prova de balas para fabricantes de veículos blindados, especialmente aqueles que buscam melhorar a proteção de veículos comerciais / civis.
No Nissan PATROL 4x4, no microônibus Volkswagen T6 TRANSPORTER e na picape Isuzu D-MAX estão instalados firewalls Deform em uma única peça, além de um piso sólido do mesmo material. O processo de conformação a quente desenvolvido pela Deform e utilizado na produção de chapas mantém uma dureza de 600 HBW.
A empresa afirma que pode restaurar as propriedades de todos os aços blindados no mercado, mantendo uma forma estruturalmente definida, enquanto as peças resultantes são muito superiores às estruturas soldadas tradicionais e parcialmente sobrepostas. No método desenvolvido pela Deform, as chapas são temperadas e revenidas após o forjamento a quente. Graças a esse processo, é possível obter formas tridimensionais que não podem ser obtidas por conformação a frio sem a obrigatória, em tais casos, "soldas que violam a integridade dos pontos críticos".
Chapas de aço formadas a quente têm sido usadas nos sistemas BAE BVS-10 e CV90 e, desde o início dos anos 1990, em muitas máquinas Kraus-Maffei Wegmann (KMW). Estão chegando pedidos para a produção de placas de blindagem tridimensionais para o tanque LEOPARD 2 e várias placas de formato para os veículos BOXER e PUMA, além de vários veículos Rheinmetall, incluindo novamente o BOXER, bem como uma escotilha para o veículo WIESEL. Deform também funciona com outros materiais de proteção, incluindo alumínio, kevlar / aramida e titânio.
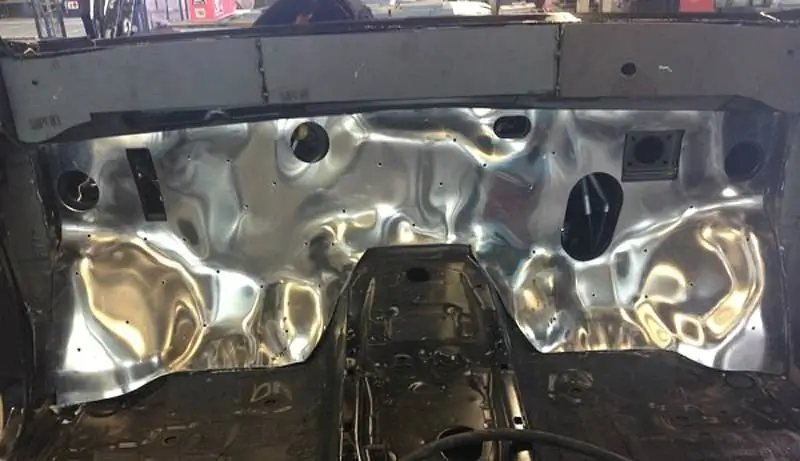
Progresso de alumínio
Quanto aos veículos blindados, pela primeira vez, a blindagem de alumínio foi amplamente utilizada na fabricação do veículo blindado de transporte de pessoal M113, que é produzido desde 1960. Era uma liga, designada 5083, contendo 4,5% de magnésio e quantidades muito menores de manganês, ferro, cobre, carbono, zinco, cromo, titânio e outros. Embora 5083 retenha sua resistência bem após a soldagem, não é uma liga tratável termicamente. Ele não tem uma resistência tão boa a balas perfurantes de 7,62 mm, mas, como testes oficiais confirmaram, ele bloqueia balas perfurantes de estilo soviético de 14,5 mm melhor do que o aço, enquanto economiza peso e adiciona a força desejada. Para este nível de proteção, a chapa de alumínio é mais espessa e 9 vezes mais resistente do que o aço com densidade inferior de 265 r / cm3, o que resulta na redução do peso da estrutura.
Os fabricantes de veículos blindados logo começaram a solicitar blindagens de alumínio mais leves, balisticamente mais fortes, soldáveis e tratáveis termicamente, o que levou ao desenvolvimento da Alcan do 7039 e posteriormente do 7017, ambos com maior teor de zinco.
Tal como acontece com o aço, a estampagem e a montagem subsequente podem afetar negativamente as propriedades de proteção do alumínio. Ao soldar, as zonas afetadas pelo calor amolecem, mas sua resistência é parcialmente restaurada devido ao endurecimento durante o envelhecimento natural. A estrutura do metal muda em zonas estreitas perto da solda, criando grandes tensões residuais no caso de erros de soldagem e / ou montagem. Consequentemente, as técnicas de fabricação devem minimizá-los, enquanto o risco de corrosão sob tensão também deve ser minimizado, especialmente quando se espera que a máquina tenha uma vida útil projetada de mais de três décadas.
A corrosão sob tensão é um processo de aparecimento e crescimento de trincas em um ambiente corrosivo, que tende a se deteriorar à medida que o número de elementos de liga aumenta. A formação de fissuras e seu subsequente crescimento ocorre como resultado da difusão do hidrogênio ao longo dos contornos do grão.
A determinação da susceptibilidade à fissuração começa com a extração de uma pequena quantidade de eletrólito das fissuras e sua análise. Testes de corrosão por tensão de baixa taxa de deformação são realizados para determinar o quão mal uma liga em particular foi atacada. O estiramento mecânico de duas amostras ocorre (uma em um ambiente corrosivo e a outra em ar seco) até que falhem e, em seguida, a deformação plástica no local da fratura é comparada - quanto mais a amostra for esticada até a falha, melhor.
A resistência à corrosão sob tensão pode ser melhorada durante o processamento. Por exemplo, de acordo com a Total Materia, que se autodenomina “o maior banco de dados de materiais do mundo”, a Alcan melhorou o desempenho do 7017 em testes de corrosão por tensão acelerada em 40 vezes. Os resultados obtidos também permitem o desenvolvimento de métodos de proteção contra corrosão de zonas de estruturas soldadas, nas quais é difícil evitar tensões residuais. Pesquisas com o objetivo de melhorar as ligas para otimizar as características eletroquímicas das juntas soldadas estão em andamento. O trabalho em novas ligas tratáveis termicamente se concentra em melhorar sua resistência e resistência à corrosão, enquanto o trabalho em ligas não tratáveis termicamente visa remover as limitações impostas pelos requisitos de soldabilidade. Os materiais mais resistentes em desenvolvimento serão 50% mais fortes do que a melhor armadura de alumínio em uso hoje.
Ligas de baixa densidade, como alumínio de lítio, oferecem cerca de 10% de economia de peso em relação às ligas anteriores com resistência à bala comparável, embora o desempenho balístico ainda não tenha sido totalmente avaliado de acordo com a Total Materia.
Os métodos de soldagem, incluindo os robóticos, também estão melhorando. Entre as tarefas a serem resolvidas estão a minimização do suprimento de calor, um arco de soldagem mais estável devido à melhoria dos sistemas de alimentação de energia e arame, bem como o monitoramento e controle do processo por sistemas especialistas.
A MTL Advanced Materials trabalhou com a ALCOA Defense, um renomado fabricante de placas de blindagem de alumínio, para desenvolver o que a empresa descreve como um "processo de conformação a frio confiável e repetível". A empresa observa que as ligas de alumínio desenvolvidas para aplicações de blindagem não foram projetadas para conformação a frio, o que significa que seu novo processo deve ajudar a evitar modos de falha comuns, incluindo rachaduras. O objetivo final é permitir que os projetistas de máquinas minimizem a necessidade de soldagem e reduzam o número de peças, de acordo com a empresa. A redução do volume de soldagem, enfatiza a empresa, aumenta a resistência estrutural e a proteção da equipe, ao mesmo tempo que reduz os custos de produção. Começando com a comprovada liga 5083-H131, a empresa desenvolveu um processo de conformação a frio com um ângulo de curvatura de 90 graus ao longo e através dos grãos, em seguida, passou para materiais mais complexos, por exemplo, ligas 7017, 7020 e 7085, alcançando também bons resultados.
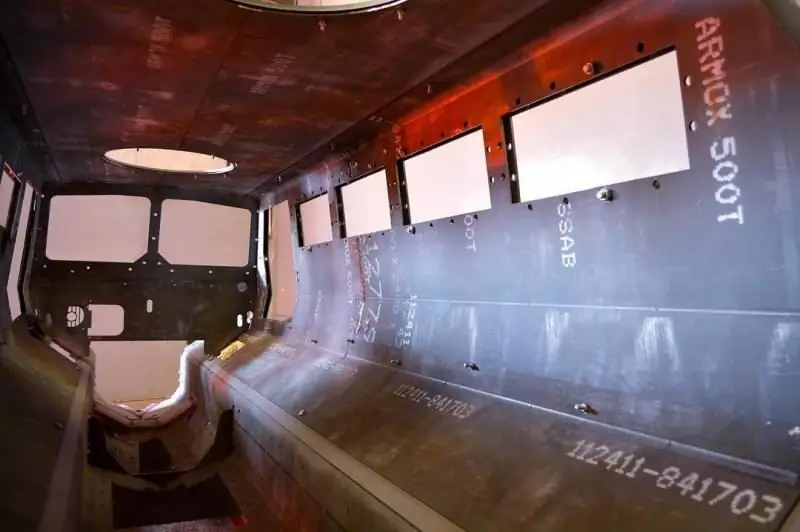
Cerâmica e compósitos
Vários anos atrás, Morgan Advanced Materials anunciou o desenvolvimento de vários sistemas de blindagem SAMAS, que consistiam em uma combinação de cerâmicas avançadas e compostos estruturais. A linha de produtos inclui blindagem articulada, lonas anti-fragmentação, cápsulas de sobrevivência feitas de compostos estruturais para substituição de cascos de metal e proteção de módulos de armas, tanto habitados como desabitados. Todos eles podem ser adaptados a requisitos específicos ou feitos sob encomenda.
Fornece proteção STANAG 4569 Nível 2-6, junto com desempenho de multi-impacto e economia de peso (a empresa afirma que esses sistemas pesam metade do peso de produtos de aço semelhantes), bem como adaptação a ameaças, plataformas e missões específicas. … Os revestimentos anti-fragmentação podem ser feitos de painéis planos pesando 12,3 kg para cobrir uma área de 0,36 m2 (cerca de 34 kg / m2) ou acessórios sólidos pesando 12,8 kg por 0,55 m2 (cerca de 23,2 kg / m2).
De acordo com Morgan Advanced Materials, blindagem adicional projetada para novas e modernizações de plataformas existentes oferece os mesmos recursos com metade do peso. O sistema patenteado oferece proteção máxima contra uma ampla gama de ameaças, incluindo armas de pequeno e médio calibre, dispositivos explosivos improvisados (IEDs) e granadas de propulsão por foguete, bem como desempenho de multi-impacto.
Um sistema de armadura "semi-estrutural" com boa resistência à corrosão é oferecido para módulos de armas (além de aplicações aéreas e marítimas) e, juntamente com a redução de peso e minimização de problemas com o centro de gravidade, ao contrário do aço, cria menos problemas de compatibilidade eletromagnética.
A proteção dos módulos de armas é um problema particular, uma vez que são um alvo atraente, uma vez que sua desativação prejudica drasticamente o domínio da tripulação sobre a situação e a capacidade do veículo de lidar com as ameaças próximas. Eles também têm optoeletrônicos delicados e motores elétricos vulneráveis. Como geralmente são instalados na parte superior do veículo, a blindagem deve ser leve para manter o centro de gravidade o mais baixo possível.
O sistema de proteção dos módulos de armas, que pode incluir vidros blindados e proteção da parte superior, é totalmente desmontável, duas pessoas podem remontá-lo em 90 segundos. As cápsulas compostas com capacidade de sobrevivência são feitas com o que a empresa descreve como “materiais resistentes e formulações poliméricas exclusivas”, que fornecem proteção contra estilhaços e podem ser reparadas em campo.
Proteção do soldado
O SPS (Soldier Protection System) desenvolvido pela 3M Ceradyne inclui capacetes e insertos em armadura para o Sistema Integrado de Proteção de Cabeça (IHPS) e VTP (Vital Torso Protection) - componentes ESAPI (Enhanced Small Arms Protective Insert) - inserto aprimorado para proteção contra armas pequenas) do sistema SPS.
Os requisitos de IHPS incluem peso mais leve, proteção auditiva passiva e proteção aprimorada contra impactos bruscos. O sistema também inclui acessórios como um componente para proteger a mandíbula de um soldado, uma viseira protetora, um suporte para óculos de visão noturna, guias para, por exemplo, uma lanterna e câmera, e proteção modular adicional de bala. O contrato, no valor de mais de US $ 7 milhões, prevê o fornecimento de cerca de 5.300 capacetes. Enquanto isso, mais de 30.000 kits ESAPI - inserções mais leves para coletes à prova de balas - serão fornecidos sob o contrato de US $ 36 milhões. A produção de ambos os kits começou em 2017.
Também no programa SPS, a KDH Defense selecionou os materiais SPECTRA SHIELD e GOLD SHIELD da Honeywell para cinco subsistemas, incluindo o subsistema de Proteção de Torso e Extremidade (TEP) a ser fornecido para o projeto SPS. O sistema de proteção TEP é 26% mais leve, o que acaba reduzindo o peso do sistema SPS em 10%. A KDH utilizará SPECTRA SHIELD, que é à base de fibra UHMWPE, e GOLD SHIELD, à base de fibras de aramida, em seus próprios produtos para este sistema.
Fibra SPECTRA
A Honeywell usa um processo patenteado de fiação e extração de fibra de polímero para incorporar a matéria-prima UHMWPE na fibra SPECTRA. Este material é 10 vezes mais resistente que o aço em termos de peso, sua resistência específica é 40% maior que a da fibra de aramida, possui ponto de fusão superior ao polietileno padrão (150 ° C) e maior resistência ao desgaste em comparação com outros polímeros, por exemplo, poliéster.
O forte e rígido material SPECTRA apresenta alta deformação na ruptura, ou seja, estica muito fortemente antes de quebrar; esta propriedade permite que uma grande quantidade de energia de impacto seja absorvida. A Honeywell afirma que os compostos de fibra SPECTRA funcionam muito bem sob impactos de alta velocidade, como balas de rifle e ondas de choque. De acordo com a empresa, “Nossa fibra avançada reage ao impacto removendo rapidamente a energia cinética da zona de impacto … ela também tem um bom amortecimento de vibração, boa resistência a deformações repetidas e excelentes características de fricção interna das fibras, juntamente com excelente resistência a produtos químicos, água e luz ultravioleta."
Em sua tecnologia SHIELD, a Honeywell espalha fios paralelos de fibras e os une, impregnando-os com uma resina avançada para criar uma fita unidirecional. Em seguida, as camadas dessa fita são colocadas transversalmente nos ângulos desejados e em uma dada temperatura e pressão, soldadas em uma estrutura composta. Para aplicações soft wearable, é laminado entre duas camadas de filme transparente fino e flexível. Como as fibras permanecem retas e paralelas, elas dissipam a energia do impacto com mais eficiência do que se fossem tecidas em um tecido.
Short Bark Industries também usa SPECTRA SHIELD no guarda-costas BCS (Ballistic Combat Shirt) para o sistema SPS TEP. A Short Bark é especializada em proteção macia, vestimentas táticas e acessórios.
De acordo com a Honeywell, os soldados escolheram os elementos de proteção feitos com esses materiais depois que demonstraram desempenho superior em relação aos seus homólogos de fibra de aramida.