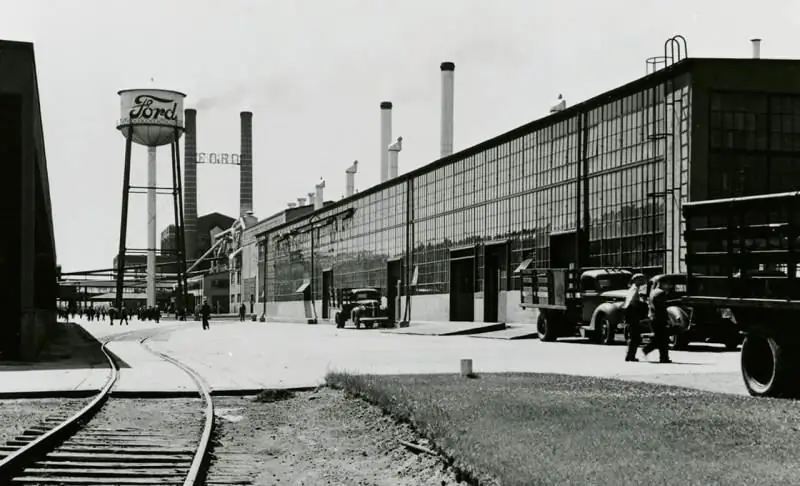
Tecnologias estratégicas
Antes de conhecer as características da produção de blindados na fábrica da Michigan Ford em Detroit (EUA), vale a pena explicar brevemente as condições em que a indústria de blindados estava se instalando na URSS. Como você sabe, tudo é aprendido por comparação.
A produção de armadura durante a Segunda Guerra Mundial foi um dos fatores mais importantes de vantagem estratégica. Com o início da guerra, a União Soviética se viu em uma posição desastrosa - toda a produção de blindados estava concentrada na parte europeia do país. O rápido avanço do exército alemão poderia paralisar completamente a produção de blindados de tanques no país. Somente à custa de esforços incríveis para evacuar parte das fábricas para o leste, no início da guerra, foi possível restaurar a produção de blindados. As principais "fábricas blindadas" eram as usinas metalúrgicas de Kuznetsk, Nizhny Tagil e Magnitogorsk.
Mas a questão não se limitou a uma simples transferência da produção para um novo local atrás da linha de frente. A maioria das novas fábricas não estava adaptada para a fundição de blindados - antes da guerra, as fábricas trabalhavam para as necessidades do Comissariado do Povo de Metalurgia Ferrosa. Wartime adicionou seus próprios ajustes. Agora que os fornos de lareira aberta muitas vezes tinham trabalhadores pouco qualificados, havia um problema agudo de falta de equipamentos especiais térmicos, de prensagem e de metalurgia. Portanto, a transferência da produção de blindados foi acompanhada por uma séria reestruturação da própria tecnologia de fundição de aço militar. Assim, foi necessário adequar a produção dos principais fornos de sola aberta para 120-180 toneladas, excluindo o processo de desoxidação por difusão. O endurecimento das placas e peças da armadura teve de ser realizado na água.
Tal simplificação não poderia deixar de afetar a qualidade da armadura recebida. Isso é especialmente verdadeiro para os mais difíceis de fabricar aço de tanque de alta dureza 8C. As primeiras amostras de placas de blindagem nos testes mostraram ardósia e camadas de fratura significativas, uma alta tendência à formação de rachaduras durante a soldagem e o endireitamento. Além disso, os testes de campo revelaram a fragilidade excessiva das amostras da armadura durante o tiro.
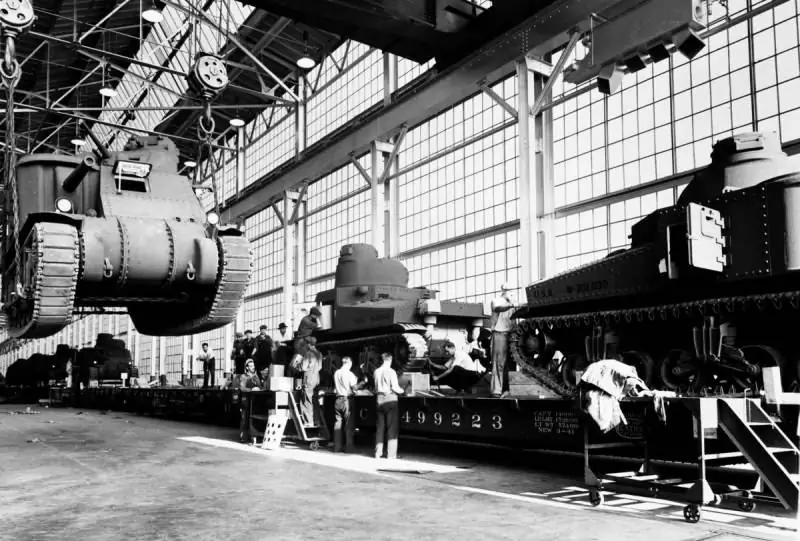
Esses defeitos não podiam ser ignorados. E no TsNII-48 especializado, eles desenvolveram uma série de melhorias. Em primeiro lugar, de agora em diante, o aço blindado deveria ser fundido apenas em fornos pré-aquecidos, após a fundição de tipos "civis" de aço. O aço tinha que ferver no banho de fundição de forno aberto por pelo menos uma hora e meia e despejado em moldes quadrados ou convexos. Além disso, os metalúrgicos deram atenção especial ao teor de enxofre do ferro-gusa original (não mais que 0,06%), bem como ao carbono e ao manganês. Em combinação com outras medidas, isso tornou possível melhorar a qualidade da armadura. Em particular, para reduzir a ardósia e camadas da fratura.
Um problema importante era a tecnologia de tratamento térmico de blindagem doméstica. Para simplificar, o endurecimento e têmpera das placas da armadura consumiam muito tempo e energia, e faltava o equipamento necessário. Era preciso simplificar o processo. A esse respeito, daremos um exemplo típico. Em 1942, os metalúrgicos de TsNII-48 conseguiram simplificar tanto o processo de preparação térmica que apenas para partes do fundo dos tanques KV e T-34 economizaram cerca de 3.230 horas-forno por 100 cascos.
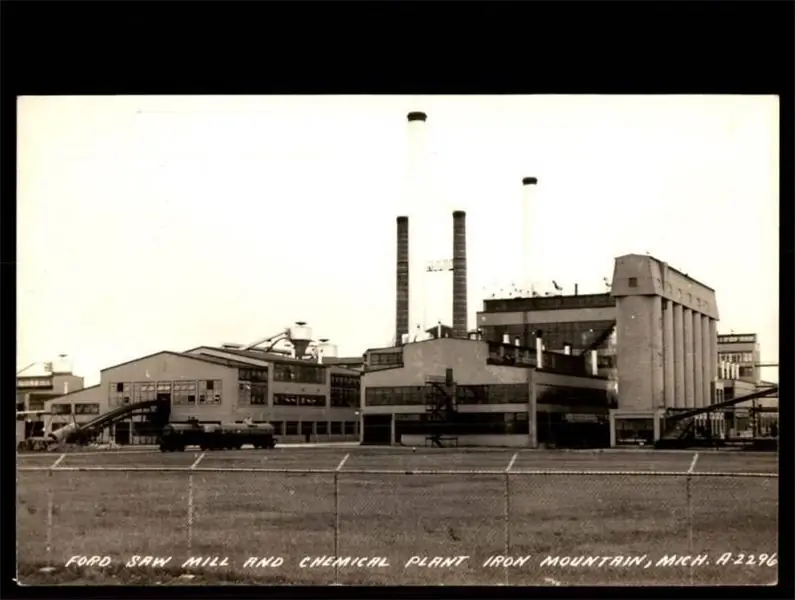
No entanto, até o final da guerra na União Soviética, as condições para a produção de blindados de tanques estrategicamente importantes estavam longe de serem necessárias. O mesmo não se pode dizer da indústria militar do parceiro ultramarino, cujo território não foi afetado pela guerra mundial. Os engenheiros metalúrgicos soviéticos tiveram que se certificar disso mais uma vez em 26 de fevereiro de 1945, 72 dias antes da Vitória.
Luxo americano
A pouco conhecida história da visita da delegação soviética à fábrica de blindados da Ford em Detroit foi anunciada por Vasily Vladimirovich Zapariy, candidato em Ciências Históricas do Instituto de História e Arqueologia do Ramo Ural da Academia Russa de Ciências. O material do cientista é baseado no relatório de metalúrgicos soviéticos sobre os resultados de uma viagem aos Estados Unidos, armazenado no Arquivo Estatal de Economia da Rússia (RGAE). Deve-se notar que o RGAE é apenas um tesouro de documentos de arquivo da época da Grande Guerra Patriótica relacionados com a produção de equipamentos e equipamentos militares. Resta apenas adivinhar quantos segredos mais o arquivo mantém nas evidências até agora classificadas.
Segundo engenheiros que voltaram de Detroit, a oficina blindada da fábrica da Ford era um edifício composto por dois vãos de 273 metros de comprimento, 30 metros de largura e cerca de 10 metros de altura. Ao mesmo tempo, a loja não cheirava armadura. Destinava-se principalmente ao tratamento térmico e corte de aço. Isso naturalmente despertou um interesse particular entre os metalúrgicos soviéticos, dados os problemas descritos acima na produção de blindados domésticos. O principal perfil de produção da oficina da Ford Motors era trabalhar com blindagens de até 76 mm de espessura. Chapas de aço tratadas termicamente foram usadas para soldar os cascos de veículos blindados leves e médios em outras fábricas em Detroit.
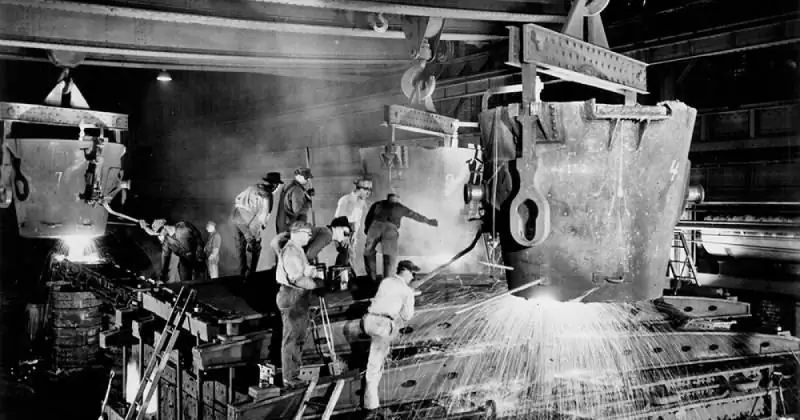
Em primeiro lugar, a mecanização do processo de produção impressionou as oficinas da Ford. Depois de derreter e laminar, as placas de blindagem foram entregues à oficina de tratamento térmico em carregadeiras de mesa hidráulicas United. Os carregadores, por sua vez, retiraram a blindagem das plataformas ferroviárias localizadas próximas à oficina. Na própria oficina, havia duas pontes rolantes projetadas para movimentar as placas de blindagem durante todas as operações tecnológicas, com exceção dos processos de têmpera.
Para criar a necessária estrutura cristalina da armadura, foram convocadas duas prensas, com um esforço de 2500 toneladas cada, cinco fornos de transportador metódico de 70 metros e cinco fornos de transportador de têmpera a gás de 100 metros. A água era fornecida às prensas de endurecimento por meio da operação de seis bombas ao mesmo tempo, bombeando mais de 3700 litros por minuto. Como escreveram os engenheiros russos, a complexidade e o custo do projeto dessas prensas, capazes de estampar e resfriar armaduras em brasa ao mesmo tempo, eram proibitivos. Ao mesmo tempo, havia dúvidas sobre a conveniência de usar prensas para armadura com espessura de 30-76 mm. Aqui, a intensidade do abastecimento de água para resfriamento veio à tona.
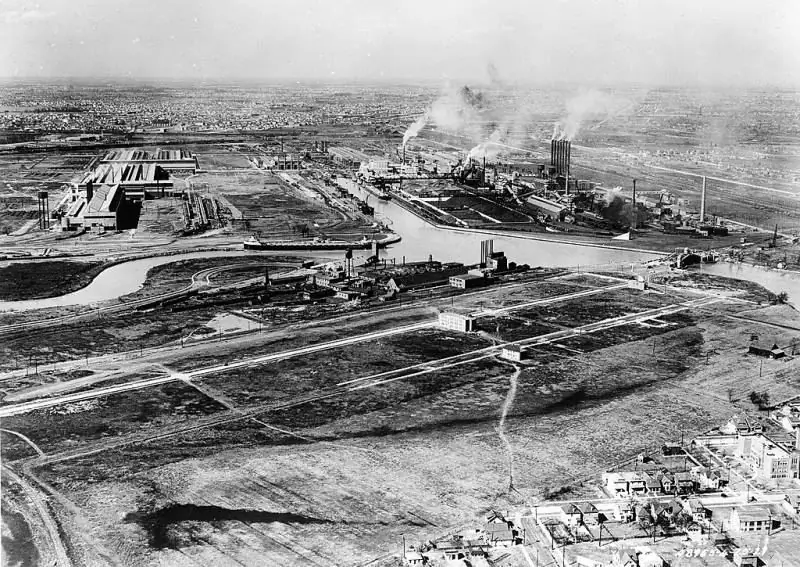
As prensas de 2.500 toneladas não eram as únicas no veículo blindado da Ford. As impressoras Toledo # 206 estavam engajadas no corte de armaduras finas e desenvolveram uma pressão de 161 toneladas. Para armaduras com espessura superior a 2,5 cm, foi utilizado exclusivamente o corte de fogo.
Durante uma visita à empresa, os metalúrgicos puderam acompanhar o processo de endurecimento de uma armadura fina à prova de balas. Ficou sob uma prensa de 1000 toneladas por 15 segundos, e então a folha foi enviada por 2,5 horas para resfriamento a 900 graus Celsius e por quatro horas de férias a 593 graus.
Toda essa riqueza técnica foi observada pelos engenheiros soviéticos, sem contar vários "pequenos acessórios": máquinas de solda, fresadoras, tesouras e similares.
A principal característica do tratamento térmico da armadura era o fluxo contínuo de produção. Em quase todos os estágios do processamento, as chapas de aço estavam em processo de movimentação em transportadores de rolos e correntes. O transportador era controlado por um console central. Em um dos últimos estágios, todas as placas de blindagem foram inspecionadas quanto ao nível de dureza Brinell. Nesse caso, a flutuação do parâmetro de teste de folha para folha deve ser mínima - não mais do que 0,2 mm.
De particular interesse para a delegação soviética eram duas máquinas de detonação, que limpavam as placas de blindagem quase após cada operação tecnológica. Esse perfeccionismo e esse luxo só podiam ser proporcionados pelos americanos, longe das agruras dos tempos de guerra.